What’s The Step-By-Step Process Of Building A Commercial Concrete Foundation?
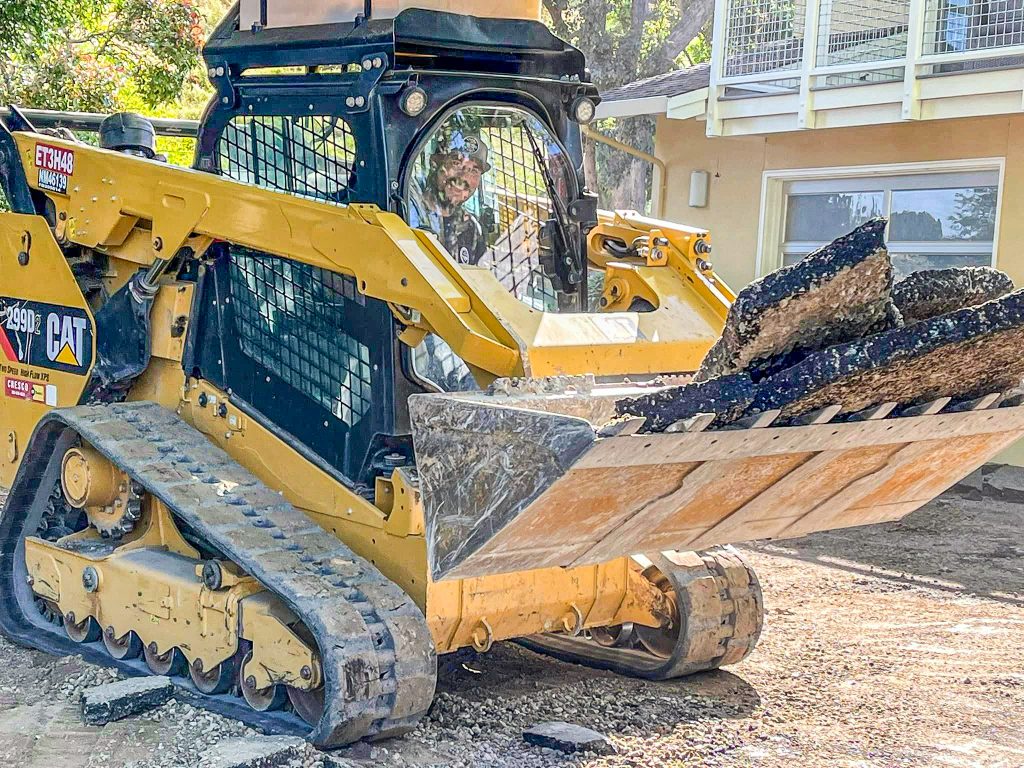
What’s The Step-By-Step Process Of Building A Commercial Concrete Foundation? Key Takeaways Begin each commercial concrete foundation job with detailed pre-construction planning. Site selection, soil testing, and appropriate budgeting up front can save unnecessary and expensive errors down the road. Never skip a systematic approach to site prep, foundation design, and construction. This method ensures that your foundation will adhere to the highest structural integrity and safety guidelines. Include a proper drainage plan during the site work phase. Additionally, employ soil stabilization techniques to protect the commercial concrete foundation from damage caused by water infiltration or migratory soil. Step 2 — Plan with high-quality materials to create a better foundation. Use best construction practices such as adequate rebar placement and extending concrete curing time to increase long-term sustainability. Establish consistent building inspections and proactive maintenance once the building is complete to detect early signs of issues and keep foundations in their best condition over the long term. Concrete foundations offer homeowners outstanding strength and fire resistance, as well as pest prevention. Expect to pay more upfront, spend more time on installation, and face restrictions on what utilities can do down the road. First, stake out the foundation with stakes and string lines. Wood forms are used to shape the slab, gravel and pipes are set up for future drainage, and rebar is laid out for strength. Then, concrete is poured, leveled, and smoothed while it’s still wet. The curing time is closely monitored to ensure the slab sets properly. Once it hardens, the forms are stripped, and the concrete is inspected for cracks or gaps. Every single step is crucial to creating a solid, long-lasting build. A detailed step-by-step guide outlines what to look out for, with clear justification for every action. Essential Pre-Construction Planning Essential pre-construction planning lays the groundwork for commercial foundation work that is efficient, safe, and budget-friendly. This phase connects conceptual early project ideas with activity on the ground. The entire process begins with an initial pre-construction meeting by the project team to establish site access, work hours, material storage locations, and quality control. Temporary railing installation, adequate signage, and ensuring workers have personal protective equipment (PPE) readily available are fundamental measures. Currently, collaboration with general contractors and construction managers provides critical advice on budgets, schedules, and the best ways to construct a building. From ideation through execution, Spaulding Concrete ensures every production material passes rigorous safety and legal regulations. Documents such as RFQs, RFPs, or ITBs are typically used to select ideal partners. The team’s combined decades of experience guarantee that all aspects—paperwork, permitting, compliance—receive detailed focus. Core planning activities include: Site meetings to set rules and quality checks Laying out safe storage and access routes Securing the work zone with fencing and signs Choosing materials that meet legal codes Handling RFQs, RFPs, and ITBs Bringing in the right contractors and managers Estimating budgets and timelines in detail Planning safety steps and emergency contacts In the long run, more time on planning saves time from delays and millions of dollars in mistakes. For instance, unobstructed access to the site increases truck efficiency, and thorough budgeting helps identify cost savings sooner. At every stage, time and money are used efficiently. No duplication of effort or expenditure. Strategic Commercial Site Selection Choosing the best location is important. Factors typically considered include the size of the land, access to major roads, availability of utilities adjacent to or near the property, and the area’s topography (flat or sloped). The site determines the kind of foundation needed—soft soils may require deep foundations like piles, while firm ground often allows the use of slabs. First, understanding the type of soil is critical. Clay, sandy, or rocky soils all require different construction approaches. Decoding Local Building Regulations Familiarity with the codes helps defend the project. Ordinances regarding depth, distance from property lines, and the appropriate placement of stormwater drains are triple-checked to avoid costly fines or having to redo completed work. With the team managing the paperwork as well, they ensure that someone else’s handiwork is maintained, making sure every step is up to par. Why Geotechnical Soil Tests Matter Soil tests indicate whether or not the land can support the proposed building. We conduct borehole investigations, compressive-strength load tests, and multi-layer soil strata checks. Clay, sand, rock—all three would give us clues about what base to get and where to pour it. These test reports provide invaluable data in deciding which design is the best, safest choice. Determining Structural Load Capacity Taking stock of the different weights the foundation will need to support—walls, equipment, and future tenants—is crucial. Load charts, previous design, and input from engineers are relied upon. Properly laying it out now ensures no undue cracking or slipping down the line. Realistic Foundation Budgeting Tips List every cost—labor, permits, materials, safety gear. Plan for soil test fees and equipment rentals Add a cushion for weather or delivery delays. Track spending weekly Use clear contracts to avoid surprise charges. By covering these costs in full at the beginning, the project remains on course no matter what changing prices or project priorities may arise. Preparing The Construction Site How you prepare the site makes a huge difference in how the entire foundation build goes. A little extra attention during pre-construction will layer in increased strength, safety, and value to a project. The better prepared the site is when you’re building, the smoother the actual build goes, with less chance of surprises or delays. Here’s what goes into it: Clear debris, brush, and old structures Mark out the foundation perimeter with stakes and string Collect geotechnical data and prepare detailed reports Grade the site to make a flat, stable base Embed utility lines—especially utility line slope and load requirements Stabilize soil with compaction or preloading, if needed Prepare for utility hook-ups, both vertically (electrical, plumbing, mechanical, comms) and horizontally (locating pole lines, etc.) Install drainage systems to keep water away Even in the digital designs, be sure to
What Happens When You Skip Proper Concrete Foundation Prep In Commercial Projects?
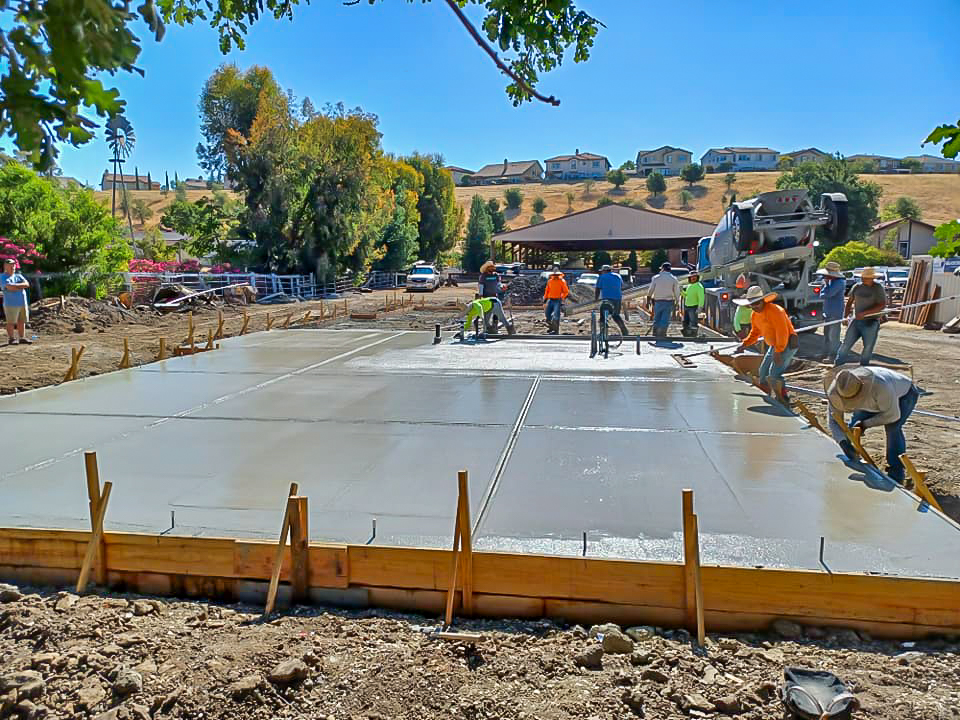
What Happens When You Skip Proper Concrete Foundation Prep In Commercial Projects? Key Takeaways Proper site preparation sets the stage for smooth, strong, and enduring commercial concrete foundations. It all begins with careful planning and making sure you have a clean and level surface. Evaluating ground conditions and soil testing will save your commercial project from skipping the proper foundation prep. These steps help make sure your plan is customized for the unique location. Providing proper grading and managing drainage are key to keeping water away from concrete. Just as importantly, these steps protect against erosion that can undermine a solid foundation over time. Building on the correct materials and proper soil compaction protects your investment long-term. Plus, adhering to specific formwork and concrete reinforcement guidelines protects the integrity of your structure. Skipping or rushing preparation increases the risk of structural problems, unexpected expenses, code violations, and safety hazards for your project. Following best industry practices, investing in expert advice, and maintaining strict quality control help you avoid common mistakes and ensure your foundation’s longevity. Skipping proper concrete foundation prep in commercial projects introduces serious risks—cracks, uneven flooring, and weak points in the slab often appear quickly. These issues can lead to binding doors, cracked walls, and expensive equipment that no longer sits level. Moisture seepage or drainage problems may also arise when the soil beneath the slab isn’t adequately compacted. Foundational errors create a ripple effect, leading to costly repairs and potential disruptions to business operations or tenant satisfaction. Cutting corners on prep work never proves beneficial when it comes to safety, building code compliance, or long-term durability. Industry best practices emphasize the importance of a thoroughly prepared foundation before any concrete is poured. The next section outlines what typically goes wrong and why proper preparation is essential. What Is Proper Site Preparation? On commercial concrete projects, site preparation lays the groundwork for a successful slab. It goes far beyond scraping away grass or shifting soil. The process begins with a thorough site inspection—reassessing the land’s topography, evaluating all slopes, and checking for potential obstructions. An even, properly compacted surface is critical to ensure structural stability and prevent future shifting or cracking. Smart, detailed planning at this stage safeguards the integrity of the foundation. Without this due diligence, cracks, settling, and other costly issues are far more likely to appear down the road. Beyond Just Clearing The Land Site preparation involves more than basic land clearing. All debris, roots, and brush must be fully removed, as leftover organic material can decay over time and create voids beneath the slab. A clean, well-prepared site is essential for protecting the foundation from erosion and prolonging the lifespan of the concrete. Implementing physical barriers and other best management practices helps prevent stormwater from washing away the site’s soil, ensuring long-term structural stability. Assessing Ground Conditions First Before work begins, it’s important to research the soil type at the site. Sandy, clay-heavy, or rocky soils each require distinct preparation methods—simple surface evaluations aren’t enough. Testing different soil layers with a shovel or probe helps determine stability. If the ground beneath the slab is weak, it can lead to cracking or settling over time. Conducting a proper soil analysis informs decisions about the appropriate concrete mix and slab thickness, ensuring a strong and lasting foundation. Why Soil Testing Is Non-Negotiable Soil tests determine whether the site contains loose fill, expansive clay, or other materials that may affect foundation performance. A qualified geotechnical engineer should review the results and recommend the most suitable preparation plan. Special attention is given to bearing capacity, compaction levels, and moisture content. Addressing these factors early helps avoid costly setbacks after the concrete is in place. Grading For Optimal Drainage The site is intentionally sloped to ensure rainwater flows away rather than underneath the slab. Proper drainage design is essential, with a gentle slope—typically no more than a 5 percent grade—directing runoff away from the structure. Even after initial grading, monitoring during heavy rainfall can reveal new pooling areas that need attention. Maintaining the correct slope reduces erosion and helps keep the slab surface dry and intact. The Essential Site Prep Checklist Whether for a big freeway job or a residential driveway, following a site prep checklist is critical for all commercial concrete jobs. This checklist takes you through each step to keep you on track with all of the moving pieces, including soil, submissions, and steel. Finally, it makes sure that everyone is working towards the same goal. A site prep checklist logs steps like soil testing, termite barriers, grading, and gear checks, so nothing falls through the cracks. In places with high termite risk, like parts of the Southeast, you need that barrier set below the finished floor line. You’ll learn important building transfer codes, including the International Building Code. Many of these codes mandate soil compaction to a minimum level of 90% of the dry density. If you don’t take these steps, you could end up with cracks or uneven slabs later. Thorough Site Clearing And Grubbing Ideally, you’d like to do this starting with a clean slate. That includes grubbing deep roots, clearing hard pan and weeds, and anything else that will eventually rot and sink. A site abandoned with stumps or brush will lead to soft spots in your slab. Crews need to maintain a clean workspace, remove rubble, and flag or paint areas for trench lines. Precise Excavation And Grading Work Avoiding the wrong depth, width, and shape when digging is key. Take, for instance, an extraordinarily simple scenario — pouring a warehouse floor. Off-level, ugly work will result in misaligned racks and machinery, causing a disaster down the line. Crews use laser levels to ensure proper grade. Proper grading will ensure less water pools on the site and will create an even slab. Achieving Correct Soil Compaction Proper compaction with rollers or plate compactors ensures the slab can bear weight. Your density gauge measures density so that you can make sure you