What Factors Should You Consider Before Starting a Stamped Concrete Project?
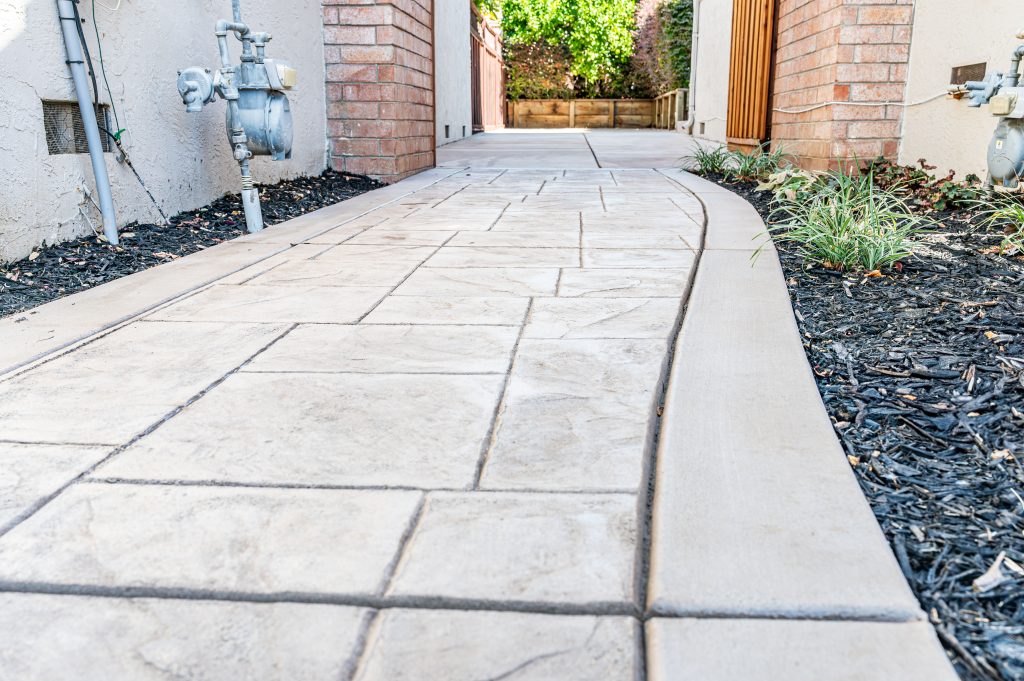
What Are The Biggest Mistakes People Make When Building Residential Retaining Walls? Consider your project scope, design possibilities, and long-term maintenance involved. Identify the space you want to cover, be it a stamped concrete patio, driveway, or walkway. These considerations will directly influence the materials and labor necessary for your project. Your stamped concrete design, patterns, and colors should harmonize with the rest of your space and your personal style without compromising function. Second, maintenance—stamped concrete requires resealing every 2–3 years to maintain its integrity and appearance. There are other considerations too. Budget planning, weather conditions, and contractor experience are huge factors in how well the project goes. Getting a clear idea on all these specifics allows you to properly budget and plan, preventing unexpected issues down the road. For expert guidance tailored to your project, consider consulting with a trusted local contractor like Spaulding Concrete. Let’s unpack that more piece by piece in the sections to follow. Key Takeaways Stamped concrete is a decorative technique that replicates natural materials like stone and wood, offering versatile design options for outdoor spaces such as patios, driveways, and walkways. Planning ahead is key to making sure your project is successful. Check your site for soil type, drainage and nearby obstacles, as well as taking precise measurements to avoid material shortages. Look at your local climate extremes, since these conditions will dictate curing, longevity, and need for maintenance. To keep the concrete surface looking fresh, choose the right sealers and additives to protect the surface. Select your patterns, textures, and colors in a way that enhances your home’s architecture and landscaping. Consider adding dark borders or contrasting accents to your concrete to create a sharper visual distinction. Plan your budget plan ahead by estimating costs for materials, installation, and upkeep. Consider future maintenance, including routine cleaning and resealing, in order to preserve appearance and longevity. We highly recommend professional installation for intricate designs to provide proper site preparation, stamping, and sealing and to prevent costly mistakes. Key Factors Before Pouring Concrete When planning a stamped concrete project, careful consideration of multiple factors can make the difference between a durable, attractive surface and one that requires frequent repairs. By considering these factors from the very beginning, you can be confident your investment will provide beautiful, long-lasting value and enjoyment to your home. Assess Your Project Site Thoroughly Begin by analyzing the type of soil and drainage conditions at your location. Expansive clay soil or insufficient drainage may cause cracks or buckled surfaces in the future. Clay-heavy soil, for instance, will need more preparation work to ensure the area is stable. Identify obstacles such as trees, utility lines, or pre-existing structures that might interfere with the layout, and measure the dimensions accurately to determine material quantities. This allows for sufficient thickness—usually 4 to 6 inches—for a strong concrete slab. Understand Local Climate Impact Weather can play a big role in curing and stamping concrete, so keep these factors in mind. In extreme heat conditions, the slab may lose its strength through rapid drying, and in colder regions, freeze-thaw cycles can lead to crumbling concrete. Select special sealers or additives, such as UV-resistant compounds, to combat regional issues. To illustrate, Luster Seal 350 is a solvent-based, low VOC, clear concrete sealer that’s designed to protect concrete surfaces from abrasives, salts and UV degradation. Plan for Proper Water Drainage Proper drainage will keep water from pooling and will extend the lifespan of your concrete. Design built-in slopes or drainage systems to move water away from the surface. Make sure landscaping does not impede runoff since diverted water can cause staining or washout. Check Necessary Permits and Codes Study your city or county’s building codes and obtain any necessary permits to prevent costly legal complications. Consulting authorities ensure compliance and prevent costly delays. Weighing Stamped Concrete’s Appeal Whether you are currently in the planning stages for a new stamped concrete project or just weighing its aesthetic appeal and functional benefits against drawbacks. This method will help you determine the best option so you can feel confident you’re making a choice that meets your goals. The Upsides: Beauty and Value Aesthetically, stamped concrete can beautifully enhance any space. With more than 75 patterns to choose from, you can get designs that replicate real stone, slate, brick, wood grain, or worn textured surfaces. This level of customization allows you to coordinate with the aesthetic of your home. Even better, it beautifully coordinates with your current hardscapes to produce a unified, finished look. A reclaimed timber texture can help you achieve a truly unique backyard patio. In the meantime, a stone-like stamped concrete finish will improve the appearance of your pool deck. Beyond good looks, the value stamped concrete brings to your property is very real. Improved curb appeal will lure in prospective buyers, helping your home stand out in a crowded market. Its versatility and durability are the most standout features. With little upkeep, such as resealing every three to five years, it has a lifespan of 25 to 30 years. In fact, it can last twice as long, in some cases, even 50 years, giving you an impressive long-term ROI. Potential Downsides to Consider Though stamped concrete holds up well against wear and tear, it’s not perfectly resistant to pitfalls. This doesn’t mean that cracking won’t happen over time—especially if the installation isn’t done properly or if the soil below moves. Upfront costs may be greater than regular concrete, though generally less than that of natural stone or brick. Proper installation by experienced professionals is crucial to avoid future repairs, ensuring the surface remains functional and visually appealing for decades. Understanding the Installation Journey What’s more, stamped concrete offers a long-lasting, beautiful option for exterior spaces. In order to ensure a successful installation, you have to be committed to meticulous planning and deployment. This process takes an average of 3 to 5 days. It’s a journey with specific manufacturing phases that require precision, quality control and conventional industry
What Should You Consider Before Hiring A Residential Retaining Wall Contractor?
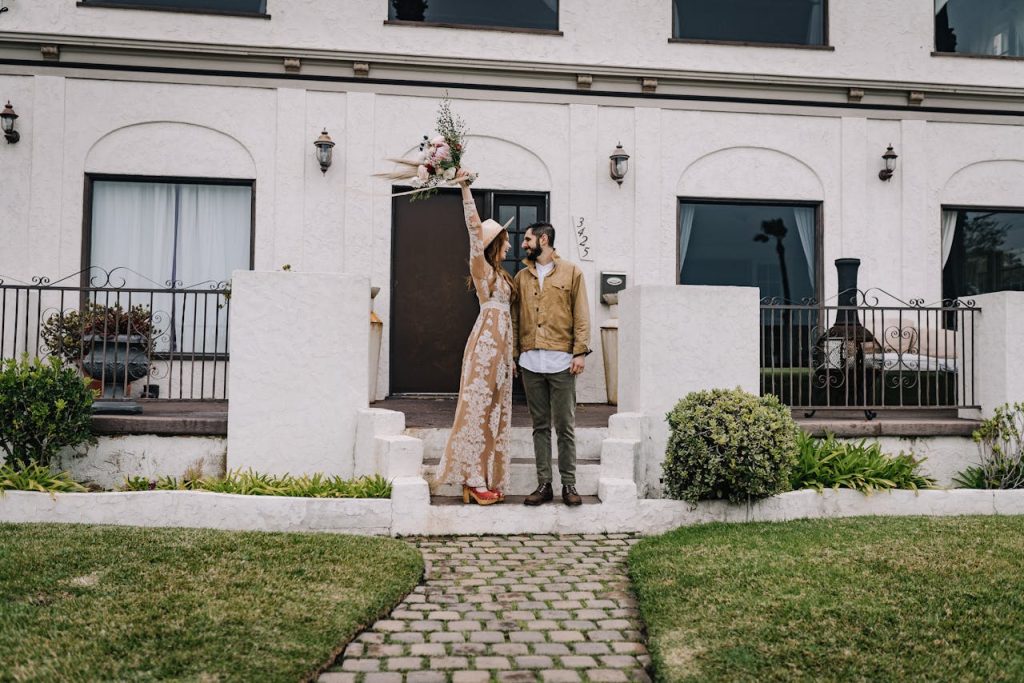
What Should You Consider Before Hiring A Residential Retaining Wall Contractor? Key Takeaways Learn about the different types of retaining walls. Gravity, cantilever, anchored, sheet p, tile walls, and more. Selecting the right type and size based on your project requirements and landscape will deliver the best results. Pay attention to key design elements, from soil pressure to drainage and wall height, for a retaining wall that can thrive in the long run. Always do your research and check contractors’ credentials, licenses, and insurance to make sure they are by local laws and will protect your investment. Soliciting written, detailed bids from several contractors. Compare costs along with materials and timelines and avoid contractor-bid sticker shock with sod story transparency in financial dealings. Review the contractor’s experience, past work portfolio, and client testimonials to gauge their expertise and reliability in retaining wall construction. Discuss design preferences, material options, and project timelines openly with your contractor to align expectations and achieve the desired outcome. Hiring the right contractor for your residential retaining wall project can make all the difference between a smooth experience and a costly headache. It’s not just about finding someone who can do the job—it’s about choosing a professional who understands your vision, meets local requirements, and communicates clearly from start to finish. In this post, we’ll walk you through the key things to consider before signing a contract. From evaluating a contractor’s experience with similar projects to checking their licensing and insurance, every detail matters. Local regulations, for instance, can significantly affect the design and installation process, so working with someone who knows the ins and outs is essential. Don’t forget to dig into their past work. Ask for a portfolio or even visit completed projects to assess quality and attention to detail. Read customer reviews, request references, and make sure you’re on the same page when it comes to timelines, costs, and materials. Taking these simple but important steps will help you avoid surprises and ensure your retaining wall is built to last. Retaining Wall Types: An Overview When designing a retaining wall, knowing the different types of retaining walls helps you choose the right option. Each wall type comes with a variety of unique advantages. To select the best one, you’ll need to take into account the site’s topography, height, and loading needs. Here, we break down the four main types of retaining walls: gravity, cantilever, anchored, and sheet pile walls. Understanding Gravity Wall Systems Gravity walls use their weight to resist the pressure of the soil behind them. Usually constructed with manufactured concrete interlocking blocks or natural stone, they work well for low-height applications, usually up to about 3 feet in height. For retaining walls shorter than 4 feet, gravity walls are the most economical and simplest option, with little to no engineering required. They work beautifully in traditional gardens and can be adapted with modern elements such as contemporary concrete blocks or with LED lighting to fit any aesthetic. These are very simple, but they are a great option for stability for small landscaping or garden projects. Exploring Cantilever Wall Designs Cantilever walls have a unique structural design. A vertical stem connects to a horizontal base slab, which distributes soil pressure very efficiently. These walls are ideal for high retention structures and sloped landscapes. Whether used in residential or commercial projects, they can be an aesthetically pleasing and durable solution where additional support is required for heavy loads. Because their design usually needs a civil engineer’s stamp and specialized permits, they are suitable for something more ornately developed with landscaping. Examining Anchored Retaining Structures Anchored walls are quite common and utilize tensioned cable or wall anchors driven into the soil for added support. These are the best options for sites subject to high-load conditions or where negative soil movement is an issue. Their structural design and durability make them ideal for more difficult terrain or taller, more residential walls that need extra strength. Discovering Sheet Pile Wall Applications Sheet pile walls, typically constructed of steel or vinyl, are often found in waterfront or soft soil environments. Installation-wise, they’re extremely fast and more budget-friendly than other types, though overall cost greatly depends on the material used and the area. These walls are particularly well-suited to shoreline projects, supplying added robustness in situations where a typical wall would wash away. Essential Design Factors When designing a residential retaining wall take special care to design factors that impact its success. This understanding is critical to designing an effective and durable building envelope. From soil type to drainage, each element dictates its overall state of stability, which is why the input of trained professionals is so essential. Analyzing Soil Pressure Dynamics The lateral earth pressures from the soil behind a retaining wall are one of the most important design factors. Soil types, clay vs sand vs silt, all respond differently to applied loads, greatly impacting wall performance. Clay has the ability to hold more water and put even more pressure on the structure. Sandy soil, on the other hand, drains easily but requires careful compaction. A geotechnical survey is critical not just to understand these abrasive conditions but to do so safely. This survey paints an accurate picture of the soil load. It informs design decisions around reinforcements like geogrid mesh or counterforts that help the wall resist different pressures that may develop. Implementing Effective Drainage Solutions Appropriate drainage systems are key to avoiding the accumulation of water, which can cause erosion or failure of the wall. Practical answers, including weep holes, perforated drainage tiles, and gravel backfill, serve to redirect groundwater away from the wall. These elements need to be considered in the design stage so you can best incorporate them into the structure. Yet, without good drainage, even a sturdy wall will fail in the long term. Ensuring Height And Structural Stability Wall height always plays a huge role in design decisions. The reason for this is simple – structures higher than three
How Do You Ensure Your Concrete Foundation Meets Local Building Codes?
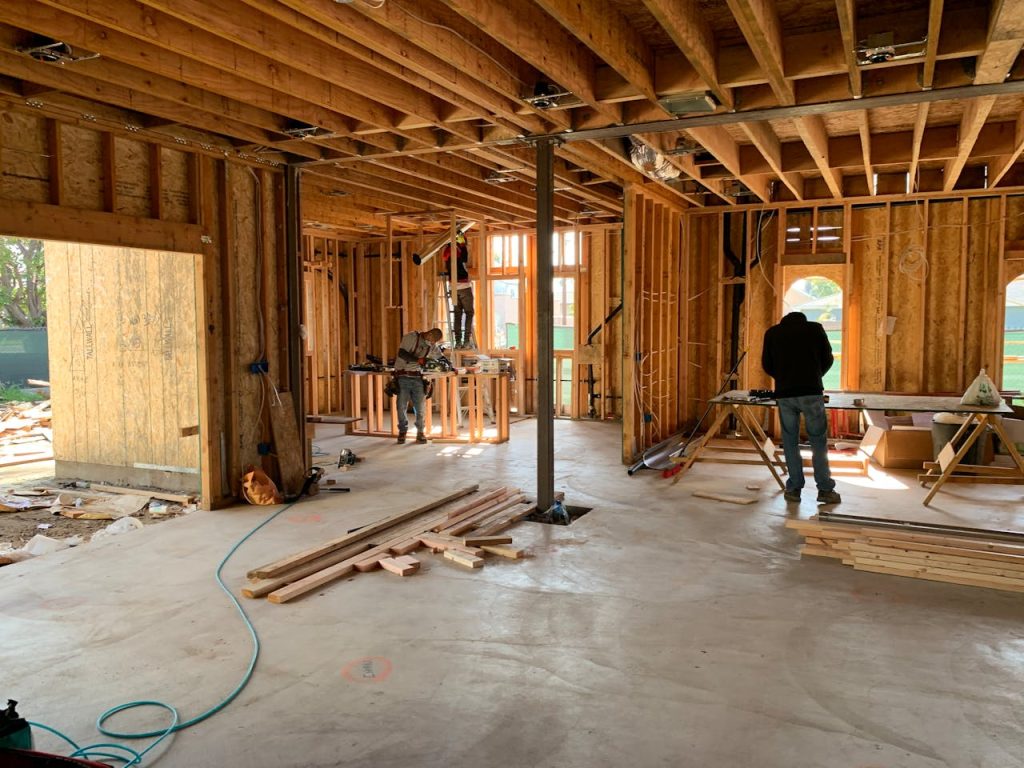
How Do You Ensure Your Concrete Foundation Meets Local Building Codes? Key Takeaways Ensuring your concrete foundation complies with local building codes is essential for safety, structural integrity, and avoiding legal issues. Ensuring compliance with local building codes safeguards builders and homeowners from risk in the future. Research local building codes and regulations that affect foundation design. Each municipality has its building codes, so doing your due diligence and keeping up with the changes is key. Make sure to secure all necessary permits and approvals ahead of breaking ground. Completing this step reduces the risk of costly delays and violations while building. Conduct site assessments, soil testing, and proper planning to ensure foundation designs meet structural and environmental requirements. These steps are critical for durability and compliance. QC, Quality Control Establish QC practice on all levels and inspection in place. Conduct concrete strength testing to verify compliance with approved plans and specifications during all phases of construction. Engage professionals such as structural engineers or geotechnical experts when faced with challenging site conditions or special design needs. Their specialized knowledge guarantees adherence to regulations and lasting structural integrity. Ensuring foundation compliance is a crucial aspect of any construction project, as it guarantees that concrete foundations meet all local building codes and regulations. These standards are in place to promote safety, structural integrity, and longevity, helping builders avoid costly mistakes and legal complications. In this post, we will explore the importance of foundation compliance and how adhering to these guidelines benefits both homeowners and contractors. By understanding and implementing compliance measures, you can protect your investment and ensure a solid, durable foundation for your structure. Foundation compliance goes beyond merely following rules—it serves as a safeguard for buildings, preventing structural failures and minimizing future repair costs. By meeting requirements set by organizations like the International Building Code (IBC) and International Residential Code (IRC), builders can ensure that a foundation can support the necessary loads while resisting environmental stresses. Key factors such as footing width, rebar reinforcement, and soil conditions all play a significant role in compliance. In this post, we will break down these elements and discuss how they contribute to the long-term stability of a building. Non-compliance with foundation regulations can lead to serious legal and financial repercussions, including hefty fines, project delays, or even demolition orders. To avoid these setbacks, it is essential to conduct thorough site assessments, secure the necessary permits, and follow strict quality control measures during construction. Additionally, staying informed about updates to local building codes and consulting with professionals can help ensure compliance from the start. In this post, we will provide practical steps and expert insights to help you navigate foundation compliance efficiently and effectively. What Is Foundation Compliance? Foundation compliance simply means making sure your concrete foundation complies with all local building codes and regulations. These codes provide a baseline to ensure that our construction projects are not just safe, but also structurally sound and built on a solid foundation. Follow these steps to set your build-up for success. They save you from making expensive errors and ensure you’ll have durability for the long haul. Compliance should not be seen simply as a bureaucratic requirement, but instead as a buffer of protection for builders, homeowners, and municipalities. Building with foundation compliance in mind goes beyond aesthetic factors and priorities. It prioritizes the safety and stability of a structure, ensuring that the foundation design process adheres to all necessary standards. For example, the foundation must meet minimum requirements outlined in standards like the International Building Codes (IBC) and International Residential Codes (IRC). Details such as the width of the footing are very important. It usually has to be two to three times the width of the wall, based on soil type and load calculations, which is crucial for establishing a strong foundation. The U.S. Building codes already require rebar reinforcement for residential footings, minimum specification of two #4 bars. These kinds of details are all important to make sure the foundation can support structural loads without risking safety. Non-compliance poses major legal and financial liability risks. Builders can be penalized with hefty fines, costly delays, or possible demolition if their terminations are found to violate the law during inspections. Consistently conducting thorough on-site inspections and pre-construction reviews are essential to identifying mistakes before they are made, ensuring the foundation repair process is straightforward if issues arise. Hiring skilled architects with a good track record and constantly checking with the local authority for any code changes are effective ways to stay on top of compliance. Green solutions such as Fox Blocks ICFs not only fulfill code mandates but advance sustainable building objectives. This mix of traits has made them a preferred option by builders themselves. Why Concrete Foundation Compliance Matters Making sure a concrete foundation is compliant with local building codes is an important aspect of any construction project. The International Building Code (IBC) and the International Residential Code (IRC) provide vital minimum standards. They are the foundation of safety, durability, and functionality across the built environment. Protection with the right compliance can strengthen the structural integrity of any building. Beyond that, it safeguards investments, prevents expensive mistakes, and maintains long-term property value. Avoid Costly Rework And Delays Failure to come into compliance can result in costly and time-consuming retrofitting. Fines, such as OSHA fines for workplace safety violations, or having to redo non-compliant foundation work can upend timelines and blow budgets. As infrastructure improvements are often complicated or costly by design, careful planning, and coordination, like consistent communication with local authorities, can avert these problems. Ensuring compliance with wind load design provisions as early as the blueprint review stage greatly reduces on-site construction hazards. Ensure Structural Longevity A compliant foundation is less vulnerable to future environmental stresses, like changing moisture content or rising temperature. Employing other advanced materials such as Ultra-High Performance Concrete (UHPC), which continues to see an increase in market demand, contributes to the extended foundation life. This allows for much