What’s The Step-By-Step Process Of Building A Commercial Concrete Foundation?
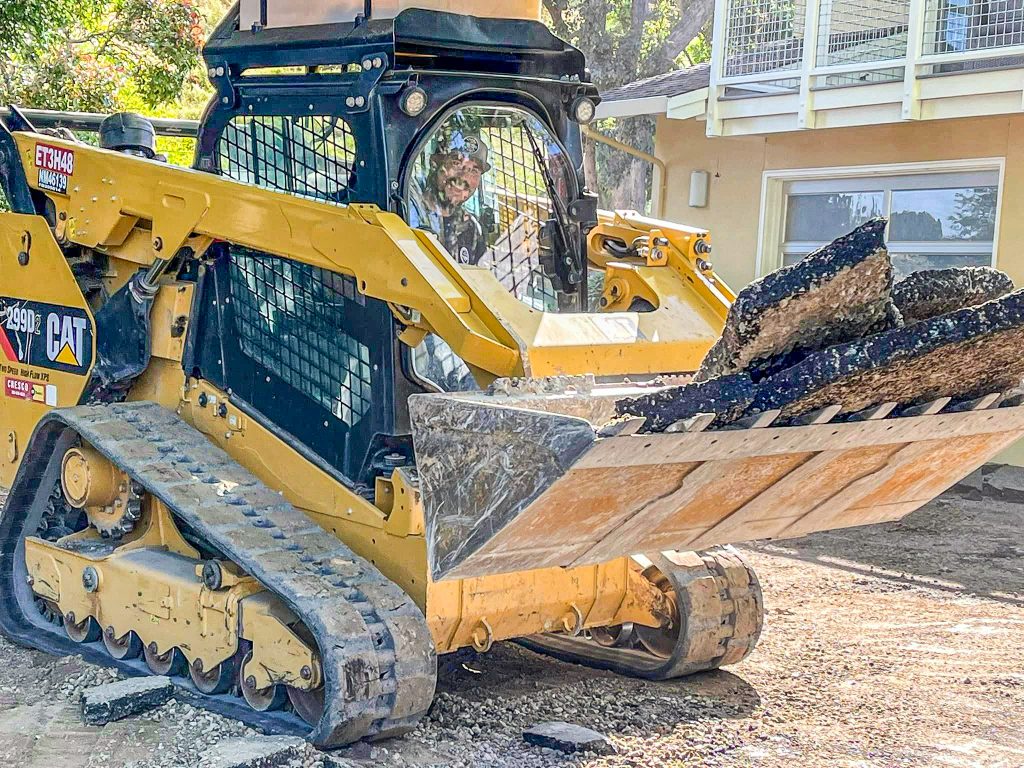
What’s The Step-By-Step Process Of Building A Commercial Concrete Foundation? Key Takeaways Begin each commercial concrete foundation job with detailed pre-construction planning. Site selection, soil testing, and appropriate budgeting up front can save unnecessary and expensive errors down the road. Never skip a systematic approach to site prep, foundation design, and construction. This method ensures that your foundation will adhere to the highest structural integrity and safety guidelines. Include a proper drainage plan during the site work phase. Additionally, employ soil stabilization techniques to protect the commercial concrete foundation from damage caused by water infiltration or migratory soil. Step 2 — Plan with high-quality materials to create a better foundation. Use best construction practices such as adequate rebar placement and extending concrete curing time to increase long-term sustainability. Establish consistent building inspections and proactive maintenance once the building is complete to detect early signs of issues and keep foundations in their best condition over the long term. Concrete foundations offer homeowners outstanding strength and fire resistance, as well as pest prevention. Expect to pay more upfront, spend more time on installation, and face restrictions on what utilities can do down the road. First, stake out the foundation with stakes and string lines. Wood forms are used to shape the slab, gravel and pipes are set up for future drainage, and rebar is laid out for strength. Then, concrete is poured, leveled, and smoothed while it’s still wet. The curing time is closely monitored to ensure the slab sets properly. Once it hardens, the forms are stripped, and the concrete is inspected for cracks or gaps. Every single step is crucial to creating a solid, long-lasting build. A detailed step-by-step guide outlines what to look out for, with clear justification for every action. Essential Pre-Construction Planning Essential pre-construction planning lays the groundwork for commercial foundation work that is efficient, safe, and budget-friendly. This phase connects conceptual early project ideas with activity on the ground. The entire process begins with an initial pre-construction meeting by the project team to establish site access, work hours, material storage locations, and quality control. Temporary railing installation, adequate signage, and ensuring workers have personal protective equipment (PPE) readily available are fundamental measures. Currently, collaboration with general contractors and construction managers provides critical advice on budgets, schedules, and the best ways to construct a building. From ideation through execution, Spaulding Concrete ensures every production material passes rigorous safety and legal regulations. Documents such as RFQs, RFPs, or ITBs are typically used to select ideal partners. The team’s combined decades of experience guarantee that all aspects—paperwork, permitting, compliance—receive detailed focus. Core planning activities include: Site meetings to set rules and quality checks Laying out safe storage and access routes Securing the work zone with fencing and signs Choosing materials that meet legal codes Handling RFQs, RFPs, and ITBs Bringing in the right contractors and managers Estimating budgets and timelines in detail Planning safety steps and emergency contacts In the long run, more time on planning saves time from delays and millions of dollars in mistakes. For instance, unobstructed access to the site increases truck efficiency, and thorough budgeting helps identify cost savings sooner. At every stage, time and money are used efficiently. No duplication of effort or expenditure. Strategic Commercial Site Selection Choosing the best location is important. Factors typically considered include the size of the land, access to major roads, availability of utilities adjacent to or near the property, and the area’s topography (flat or sloped). The site determines the kind of foundation needed—soft soils may require deep foundations like piles, while firm ground often allows the use of slabs. First, understanding the type of soil is critical. Clay, sandy, or rocky soils all require different construction approaches. Decoding Local Building Regulations Familiarity with the codes helps defend the project. Ordinances regarding depth, distance from property lines, and the appropriate placement of stormwater drains are triple-checked to avoid costly fines or having to redo completed work. With the team managing the paperwork as well, they ensure that someone else’s handiwork is maintained, making sure every step is up to par. Why Geotechnical Soil Tests Matter Soil tests indicate whether or not the land can support the proposed building. We conduct borehole investigations, compressive-strength load tests, and multi-layer soil strata checks. Clay, sand, rock—all three would give us clues about what base to get and where to pour it. These test reports provide invaluable data in deciding which design is the best, safest choice. Determining Structural Load Capacity Taking stock of the different weights the foundation will need to support—walls, equipment, and future tenants—is crucial. Load charts, previous design, and input from engineers are relied upon. Properly laying it out now ensures no undue cracking or slipping down the line. Realistic Foundation Budgeting Tips List every cost—labor, permits, materials, safety gear. Plan for soil test fees and equipment rentals Add a cushion for weather or delivery delays. Track spending weekly Use clear contracts to avoid surprise charges. By covering these costs in full at the beginning, the project remains on course no matter what changing prices or project priorities may arise. Preparing The Construction Site How you prepare the site makes a huge difference in how the entire foundation build goes. A little extra attention during pre-construction will layer in increased strength, safety, and value to a project. The better prepared the site is when you’re building, the smoother the actual build goes, with less chance of surprises or delays. Here’s what goes into it: Clear debris, brush, and old structures Mark out the foundation perimeter with stakes and string Collect geotechnical data and prepare detailed reports Grade the site to make a flat, stable base Embed utility lines—especially utility line slope and load requirements Stabilize soil with compaction or preloading, if needed Prepare for utility hook-ups, both vertically (electrical, plumbing, mechanical, comms) and horizontally (locating pole lines, etc.) Install drainage systems to keep water away Even in the digital designs, be sure to
How Do You Know If You’re Choosing The Wrong Type Of Commercial Concrete Foundation?
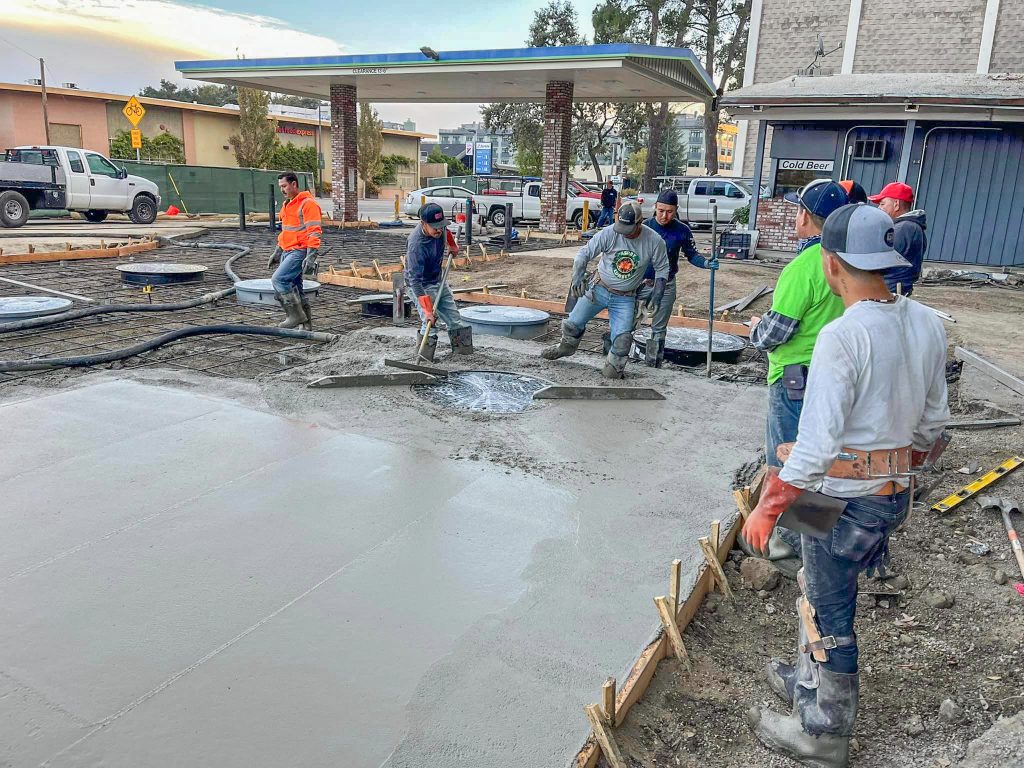
How Do You Know If You’re Choosing The Wrong Type Of Commercial Concrete Foundation? Key Takeaways How to know if the wrong type of commercial concrete foundation is being selected? The choice depends on the structure’s scale, ground conditions, and loading needs to maintain structural integrity. Regular monitoring for visible cracks, uneven settling, and moisture issues helps detect foundation problems early and prevent costly damage. Conducting thorough soil tests and understanding local building codes are critical steps before selecting a foundation type for any commercial project. Working side by side with foundation engineering experts and employing pre-construction site testing methods ensures costly construction phase missteps are avoided. Prioritizing long-term durability improves the ability to achieve a foundation that lasts. Planning for future maintenance helps avoid repeated costly repairs. Continuous learning about new foundation techniques and technologies enhances the efficiency, safety, and performance of construction projects. Choosing the wrong type of commercial concrete foundation shows up in signs like cracks in the floors, walls that start to bow, and doors that stick or won’t close right. Common issues include sagging cracks in interior floors, standing water along the edge of the building, or flaking delamination at the concrete cornice. These problems result from an incorrect choice of foundation type in relation to the soil or loading requirements of the site. Active pipe leaks or unusual noises coming from below serve as another major alarm. Over time, minor defects escalate into major renovation projects. This post breaks down the most common warning signs and shares what to check so issues can be spotted early, keeping the building safe and steady. What Are Commercial Concrete Foundations? They hold up all that weight and make sure everything stays nice and even. Concrete foundations are made entirely of concrete, a durable and resilient material that provides a firm foundation. Typically, they are much deeper than they are wide. Generally, their depth-to-width aspect ratio is greater than 4 to 5. Their arrangement typically consists of a slab on grade, commonly a 4 to 6-inch-thick concrete slab. This sturdy foundation allows the building to thrive for decades. With the proper type of foundation, heavy or light, the building will be safe, steady, and secure, regardless of the load above or the soil underneath. Defining Shallow Foundation Systems Shallow foundations are located near the ground surface, making them relatively inexpensive and easy to install. The two most typically used types are slab-on-grade and spread footings. Slab-on-grade slab foundations are a single slab, usually four to six inches thick, that sits directly on the ground. Spread footings would employ concrete pads to distribute the load across a larger surface. For light buildings, such as low-rise office spaces or small retail storefronts, builders usually opt for shallow foundations. Approximately 80% to 90% of all one- and two-story commercial buildings utilize this type of foundation. These systems allow for lower unit costs and a faster overall build. Exploring Deep Foundation Systems Deep foundations extend far down to stable soil or bedrock. Types of commercial concrete foundations include pile and drilled shaft foundations. While piles are generally long columns driven deep into the ground, drilled shafts are, as the name suggests, holes filled with concrete. Consider heavy structures such as skyscrapers or locations built on soft soil—all scenarios that require deep foundation support. Deep foundations take on larger loads and more problematic soil. Key Differences: Shallow VS. Deep Shallow foundations don’t reach as great a depth but are more appropriate for light loads and strong, stable soil. Deep foundations extend deep underground to reach sturdy base layers and support heavier loads. Shallow types are less expensive and can be constructed faster, but deep types are better for taller and heavier buildings. Signs You Chose The Wrong Foundation Identifying the wrong type of commercial concrete foundation from the start goes a long way in protecting your building’s longevity and structural integrity. You can read the signs as they happen in person. Cracking, leaking, and premature deterioration result when the foundation is wrong for the intended use. By paying careful attention to your foundation, you can identify small problems before they become large ones. 1. Visible Cracks And Settlement Issues Cracks in walls or floors make the list as the number one sign. These cracks may be caused by damage from extreme heat, plumbing leaks, tree roots, or when concrete dries too quickly. Vertical cracks typically indicate foundation settlement. Slab-on-grade footing cracks are never seen since the footing is below the ground and hidden. Any movement is quickly revealed through sloped floors or doors that stick. Swift action from an expert prevents more costly issues from accumulating over time. 2. Unexpected Moisture Or Water Problems When water comes creeping in, that’s a sign your drainage system has failed. All of that stuff is heavy rain, bad run-off, or the absence of waterproofing that allows moisture to come in. That undermines both the foundation and what it allows to stand above it. You need that waterproofing underneath yesterday if you start noticing moisture coming through or puddles forming. 3. Structure Performs Below Expectations A building that is sinking, wobbly, or moving around indicates the wrong foundation. If the concrete base doesn’t adequately compensate for the soil conditions or weight of the building, the entire system operates suboptimally. Having a keen eye on your foundation choice prevents issues from developing into roadblocks that hinder your progress. 4. Foundation Exceeds Maintenance Needs If it requires a lot of fixes—paving over, raising, filling in, and repairing—it indicates the design was probably the wrong appropriateness. Foundational foundations should make maintenance minimal. When maintenance is consistently forced to take the back seat, that’s something deserving of a more serious examination. 5. Early Material Degradation Observed If floors, beams, or other supports begin wearing prematurely, your foundation is likely misaligned. Salt, water, and weather exacerbate this process. Recognizing compromised components indicates it’s time to take a closer look at the foundation. 6. Mismatched Foundation And Soil Behavior Getting the
What Questions Should You Ask Before Hiring A Commercial Concrete Foundation Contractor?
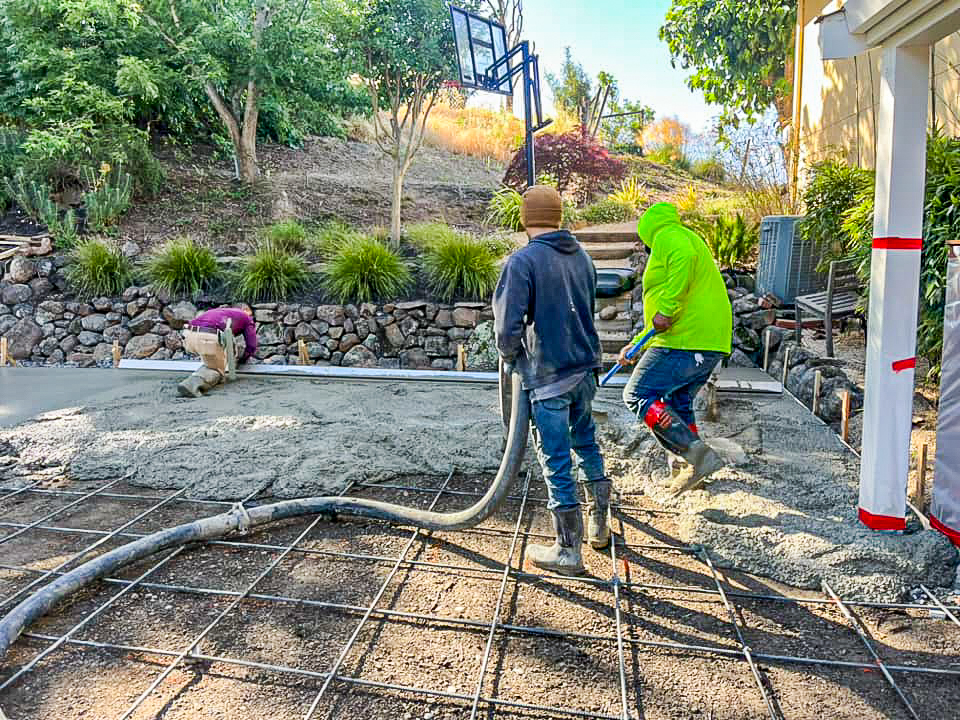
What Questions Should You Ask Before Hiring A Commercial Concrete Foundation Contractor? Key Takeaways Make sure your commercial concrete foundation contractor has a state license. Confirm that they carry insurance and bonding to keep your interests protected and encourage adherence to the rules. Ask for examples that demonstrate the contractor’s experience with projects similar to yours. Request a list of client references to obtain information about their reputation and performance. Well in advance, settle on the contractor’s overall project execution strategy, including precise timelines, detailed material selection, and quality control processes. Inspect the contractor’s on-site management habits. Make daily crew schedules, equipment safety protocols, and site debris removal a priority to limit project disruptions and maintain site safety. Ask for a detailed cost estimate to avoid surprises and hidden fees. Inquire about payment schedules and how to manage changes or additions to the project once work has begun. Don’t sign until you’ve familiarized yourself with any workmanship or material warranties or guarantees. Understanding this information will better prepare you to protect your investment after the project is finished. The questions to ask before hiring a commercial concrete foundation contractor should focus on the company’s experience, licensing and insurance, past project references, and timeline for completion. Ensuring the contractor has a proven track record with similar work is essential. Additionally, verify that they are adequately insured. Inquire about the crew members, the materials they plan to use, and whether they adhere to local codes. Asking about the total costs of the project and its payment plan helps set expectations. It’s also important to ask about their process for addressing delays or changes that may arise during the project to avoid future headaches. In the coming sections, these questions will be unpacked in detail, providing insight into how to choose wisely. Verify Contractor Legitimacy First First, before you decide on a new commercial concrete foundation contractor, do your homework and verify that they’re legitimate. You’re looking for the one who plays by the book, protects your investment, and operates a great business. Hiring someone who doesn’t have the right paperwork is a huge liability. All of these points make it imperative that they can substantiate their proposal with supporting evidence. As a large majority of private businesses fail within 15 years, it’s best to ensure these fundamentals are covered to keep you out of hot water. Confirm State Licensing Details Request that the contractor provide evidence of their state license. Each state determines its guidelines for commercial concrete projects. A valid license shows that the contractor is following those guidelines. Search for their license number on your state’s licensing board website. Additionally, the board will include any past violations or complaints on file. This indeed provides you with a better idea of their history. Confirm they’ve completed projects similar to yours in your metropolitan area. For example, if you need a foundation for a two-story office, ask if they have built something like that nearby. Check if they have a physical headquarters, and not just a P.O. box or a cell phone. Check Comprehensive Insurance Coverage You need to be sure the contractor has adequate coverage. This includes any harm to your house as well as injury to their workers. Require proof of liability insurance and ensure that it covers the complete project. Workers’ comp should protect all workers. Read through the policy closely, so you understand what is covered and what is not. A contractor that has a BBB accreditation and good rating usually has up-to-date policies. Ask About Project Bonding Inquire if the contractor is properly bonded. A bond is a certain amount of money that’s reserved for you if the contractor fails to complete the job. Request documentation that demonstrates their bond is current. A written warranty policy and candid responses regarding bonding demonstrate that they operate an honest company. Assess Relevant Commercial Experience That’s why, when you search for a commercial concrete foundation contractor, you’re looking for evidence that they have a deep knowledge of this discipline. Questions to ask: Each of them has years in business, and whether they have achieved any industry-specific certifications to better understand their know-how. Specialty contractors with a wealth of experience, like Spaulding Concrete, know the exact steps required for every job. Our deep industry expertise ensures that we arrive with the best tools and materials, guaranteeing the highest quality work on every project. With a proven history of successful commercial foundation projects, Spaulding Concrete provides peace of mind through our outstanding reputation, deep bench strength, and dedication to excellence. They show up with the best tools and use the best materials we have. Their deep bench strength, outstanding reputation, and proven history of quality work make them unique. You get more peace of mind knowing that they have completed tasks like your own. You are even more confident if they have established credibility with other industry players. Request Similar Project Examples Begin by simply requesting a portfolio that includes projects similar to yours. We know you want to see photos, specs, and a quick write-up detailing what each job entailed. See if their previous experience matches your project’s scale and requirements. A contractor who has previously poured foundations for large commercial retail pads or office buildings shows their capacity to do the larger projects. They absorb project complexity, large pours, heavy loads, and deadlines. If you notice an alignment of project types—warehouses, schools, and medical centers—you’ll realize that they are capable of meeting multiple priorities. Can You Provide Client References? Request the names and contact information of previous clients. Don’t hesitate to inquire about whether the job was completed on schedule. You might ask how the team ensured the safety of the site and what large or unexpected issues came up. Clients will open up about minor issues but focus on how the contractor went above and beyond to resolve them. This provides you with a transparent window to understand how the contractor operates daily. Review Past Commercial Case
What Happens When You Skip Proper Concrete Foundation Prep In Commercial Projects?
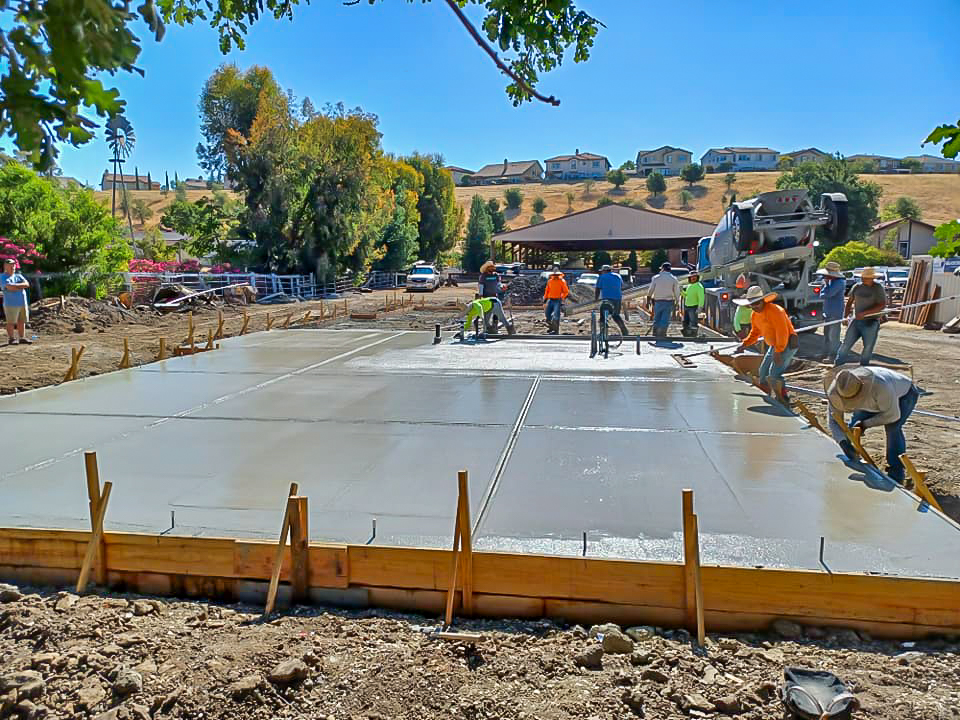
What Happens When You Skip Proper Concrete Foundation Prep In Commercial Projects? Key Takeaways Proper site preparation sets the stage for smooth, strong, and enduring commercial concrete foundations. It all begins with careful planning and making sure you have a clean and level surface. Evaluating ground conditions and soil testing will save your commercial project from skipping the proper foundation prep. These steps help make sure your plan is customized for the unique location. Providing proper grading and managing drainage are key to keeping water away from concrete. Just as importantly, these steps protect against erosion that can undermine a solid foundation over time. Building on the correct materials and proper soil compaction protects your investment long-term. Plus, adhering to specific formwork and concrete reinforcement guidelines protects the integrity of your structure. Skipping or rushing preparation increases the risk of structural problems, unexpected expenses, code violations, and safety hazards for your project. Following best industry practices, investing in expert advice, and maintaining strict quality control help you avoid common mistakes and ensure your foundation’s longevity. Skipping proper concrete foundation prep in commercial projects introduces serious risks—cracks, uneven flooring, and weak points in the slab often appear quickly. These issues can lead to binding doors, cracked walls, and expensive equipment that no longer sits level. Moisture seepage or drainage problems may also arise when the soil beneath the slab isn’t adequately compacted. Foundational errors create a ripple effect, leading to costly repairs and potential disruptions to business operations or tenant satisfaction. Cutting corners on prep work never proves beneficial when it comes to safety, building code compliance, or long-term durability. Industry best practices emphasize the importance of a thoroughly prepared foundation before any concrete is poured. The next section outlines what typically goes wrong and why proper preparation is essential. What Is Proper Site Preparation? On commercial concrete projects, site preparation lays the groundwork for a successful slab. It goes far beyond scraping away grass or shifting soil. The process begins with a thorough site inspection—reassessing the land’s topography, evaluating all slopes, and checking for potential obstructions. An even, properly compacted surface is critical to ensure structural stability and prevent future shifting or cracking. Smart, detailed planning at this stage safeguards the integrity of the foundation. Without this due diligence, cracks, settling, and other costly issues are far more likely to appear down the road. Beyond Just Clearing The Land Site preparation involves more than basic land clearing. All debris, roots, and brush must be fully removed, as leftover organic material can decay over time and create voids beneath the slab. A clean, well-prepared site is essential for protecting the foundation from erosion and prolonging the lifespan of the concrete. Implementing physical barriers and other best management practices helps prevent stormwater from washing away the site’s soil, ensuring long-term structural stability. Assessing Ground Conditions First Before work begins, it’s important to research the soil type at the site. Sandy, clay-heavy, or rocky soils each require distinct preparation methods—simple surface evaluations aren’t enough. Testing different soil layers with a shovel or probe helps determine stability. If the ground beneath the slab is weak, it can lead to cracking or settling over time. Conducting a proper soil analysis informs decisions about the appropriate concrete mix and slab thickness, ensuring a strong and lasting foundation. Why Soil Testing Is Non-Negotiable Soil tests determine whether the site contains loose fill, expansive clay, or other materials that may affect foundation performance. A qualified geotechnical engineer should review the results and recommend the most suitable preparation plan. Special attention is given to bearing capacity, compaction levels, and moisture content. Addressing these factors early helps avoid costly setbacks after the concrete is in place. Grading For Optimal Drainage The site is intentionally sloped to ensure rainwater flows away rather than underneath the slab. Proper drainage design is essential, with a gentle slope—typically no more than a 5 percent grade—directing runoff away from the structure. Even after initial grading, monitoring during heavy rainfall can reveal new pooling areas that need attention. Maintaining the correct slope reduces erosion and helps keep the slab surface dry and intact. The Essential Site Prep Checklist Whether for a big freeway job or a residential driveway, following a site prep checklist is critical for all commercial concrete jobs. This checklist takes you through each step to keep you on track with all of the moving pieces, including soil, submissions, and steel. Finally, it makes sure that everyone is working towards the same goal. A site prep checklist logs steps like soil testing, termite barriers, grading, and gear checks, so nothing falls through the cracks. In places with high termite risk, like parts of the Southeast, you need that barrier set below the finished floor line. You’ll learn important building transfer codes, including the International Building Code. Many of these codes mandate soil compaction to a minimum level of 90% of the dry density. If you don’t take these steps, you could end up with cracks or uneven slabs later. Thorough Site Clearing And Grubbing Ideally, you’d like to do this starting with a clean slate. That includes grubbing deep roots, clearing hard pan and weeds, and anything else that will eventually rot and sink. A site abandoned with stumps or brush will lead to soft spots in your slab. Crews need to maintain a clean workspace, remove rubble, and flag or paint areas for trench lines. Precise Excavation And Grading Work Avoiding the wrong depth, width, and shape when digging is key. Take, for instance, an extraordinarily simple scenario — pouring a warehouse floor. Off-level, ugly work will result in misaligned racks and machinery, causing a disaster down the line. Crews use laser levels to ensure proper grade. Proper grading will ensure less water pools on the site and will create an even slab. Achieving Correct Soil Compaction Proper compaction with rollers or plate compactors ensures the slab can bear weight. Your density gauge measures density so that you can make sure you
Are You Choosing The Right Commercial Concrete Foundation Contractor Or Just The Cheapest?
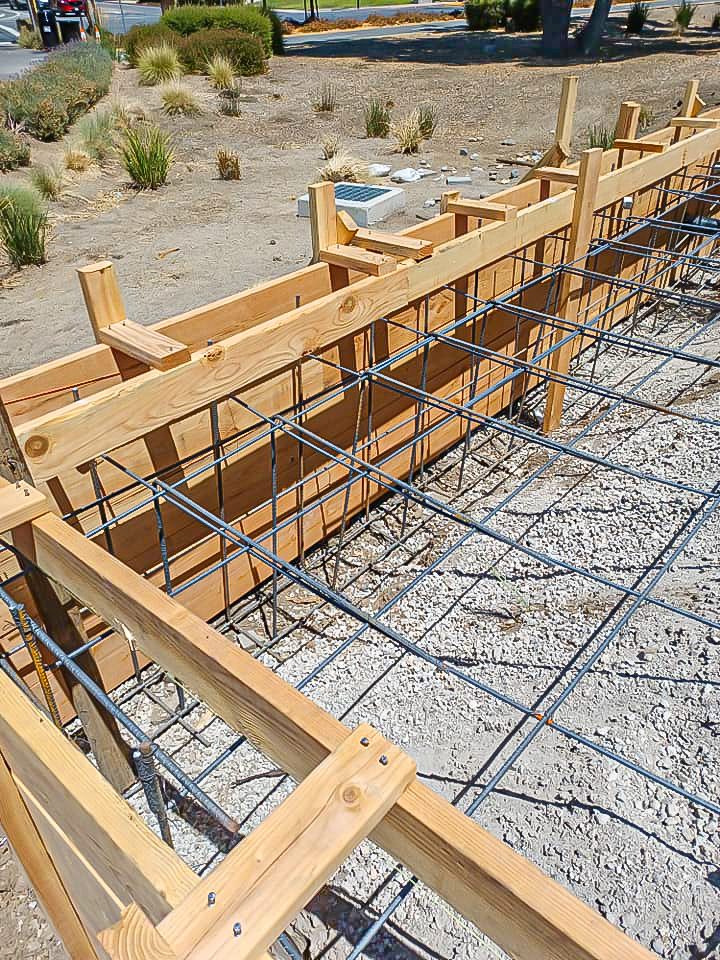
Are You Choosing The Right Commercial Concrete Foundation Contractor Or Just The Cheapest? Key Takeaways Checking licenses, insurance, and industry certifications protects my investment and gives me peace of mind that the contractor operates with a high level of professionalism. Reviewing past projects, client references, and local reputation lets me assess if the contractor is a good fit for my needs. Bids should be compared based on materials and methods proposed, and overall value, not price alone, to prevent hidden costs and extensive future repair. Understanding contract terms, warranties, and communication expectations helps prevent misunderstandings and ensures accountability. Making quality workmanship and open communication a priority helps ensure a successful project outcome with durable, long-lasting results. Selecting the right commercial concrete foundation contractor ensures quality work, clear timelines, and a job done correctly the first time. A reputable contractor brings the right team, uses high-quality materials, and is well-versed in handling city codes and site-specific challenges. In this post, we’ll discuss why choosing a contractor based solely on the lowest bid can lead to cracks, delays, or unforeseen costs in the future. It’s crucial to select a contractor who provides detailed bids, offers documentation of previous work, and has excellent references from projects similar to yours. Request copies of licenses and insurance, and evaluate their communication skills. A reliable contractor will demonstrate professionalism and follow through on commitments. Why Cheapest Isn’t Always Best When selecting a commercial concrete foundation contractor, you typically begin with the bottom line. If you’re an agency, a lower bid might look like a slam dunk. It’s always smart to look beneath the surface and understand precisely what you are receiving. When you get one quote that is a third of the cost of the rest, it’s not a steal, it’s a red flag. It’s a great signal to dig deeper and ask more questions. Low bids usually mean taking a hit on labor or using thin slabs or cheap materials. These decisions can lead to significant cost increases down the line. The Hidden Costs Of Low Bids A contractor willing to accept rock-bottom prices may go with less expensive mix designs or cut corners and omit the proper reinforcements. Instead, you can expect to start noticing cracks, shoddy work, drainage issues, etc. Much, much earlier. If the job requires repairs down the line, such as re-patching or even worse, replacing entire sections, that expense is quickly mitigated. Delays go hand-in-hand with low-cost providers as well. Missed deadlines or added procedures can result in significant disruptions to your business, sometimes leaving you with unforeseen costs. Long-Term Value VS. Short-Term Savings A strong, deep foundation holds steady in the shifting sands of time and weather. In the end, paying just a little more for a contractor who has the right skills and tools will pay off in fewer repair and maintenance costs. In the U.S., the typical concrete driveway costs $4–15/sf. Going with the lowest bidder often causes contractors to incur added costs later. It’s not from the cheapest price, but rather from a quality repair executed properly on the first go-around. Risks Of Inexperienced Foundation Work In addition, less-experienced contractors may cut corners, forget important steps, leave out important permits, or lack adequate insurance. Failing to address this may result in downstream threats such as out-of-court settlements, water damage, or litigation. For your safety, it’s worth the price to go with a licensed team that has proven expertise. Verify Contractor Credentials First Selecting a concrete foundation contractor for a large commercial project requires much more than a fast price comparison. You want to know that the team on your site can meet all state and local rules and keep your project safe from start to finish. Get ahead by organizing your documents. Get your licenses and insurance in order and have a full set of professional references—a track history without complaints or red flags. These steps help you spot the difference between someone ready for the job and someone who just wants to cut corners. Check Essential Licenses And Insurance Each state requires different licenses for different types of concrete work. Compile a list of what’s required in your jurisdiction, such as general contractor and specialty concrete licensing. If you are unsure, always ask the contractor for proof and verify with your local building department. For insurance, both liability and workers’ comp are crucial. Liability protects you from damage to other property or injuries that occur on the job site, and workers’ comp will kick in if a crew member is injured. Take it from us—ALWAYS ask for proof. An experienced, trustworthy contractor provides certificates without fuss. Understand BBB Accreditation Significance The Better Business Bureau (BBB) provides an up-front and transparent view of how a contractor interacts with their clients. Accreditation demonstrates that they maintain a culture of honesty and adhere to ethical business practices. Check their BBB rating, if complaints start appearing, and what former customers have to say. A good rating translates into fewer hassles and more trust. Look For Industry Certifications Membership or certifications from organizations such as the American Concrete Institute demonstrate the contractor’s commitment to staying current with training and standards. These badges indicate that they’re always learning innovative ways to approach projects and that they place an emphasis on quality. You are looking for someone who goes beyond learning the basics, someone who advances their skills. Evaluate Contractor Experience And Fit When you search for any commercial concrete foundation contractor, experience in the industry counts. Contractors who have been in business for at least five years tend to show a steadier hand. They have a better picture of what these projects need. You want someone who knows the ins and outs of local building codes and can spot the small details that make a job right for your site. A great fit is a contractor who has notable experience with jobs like yours. This involves understanding the scope of the work, not just the overall size of the
What’s The Best Commercial Concrete Foundations Contractor In Walnut Creek, California?
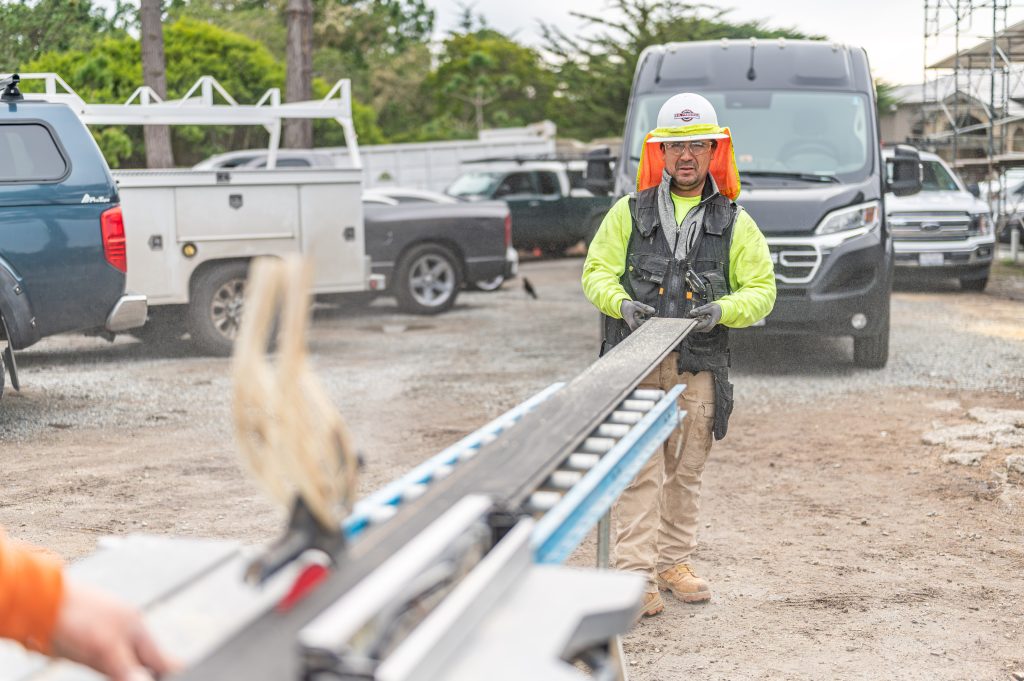
What’s The Best Commercial Concrete Foundations Contractor In Walnut Creek, California? About Walnut Creek, California, And What To Expect From A Commercial Concrete Foundations Contractor Nestled in the shadow of Mt. Diablo and a stone’s throw from the Bay Area’s bustling metropolises, Walnut Creek, California, is more than just a charming city with a thriving downtown. It’s a hub of suburban sophistication, natural beauty, and steady commercial growth. As more businesses plant their roots in Walnut Creek, the demand for robust, durable infrastructure grows — and that begins, quite literally, from the ground up. That’s where commercial concrete foundation contractors come in. In this comprehensive guide, we’ll explore the city of Walnut Creek—its appeal, history, economy, and commercial climate—and then dig into what business owners, developers, and investors can expect when working with commercial concrete foundation contractors in the area. A. The Heart Of The East Bay – An Introduction To Walnut Creek, California A City With Roots And Vision Walnut Creek began as a small settlement in the mid-1800s and blossomed into a prominent East Bay city over the decades. Originally part of several Mexican land grants, the area attracted settlers during California’s Gold Rush. Officially incorporated in 1914, Walnut Creek has evolved from a sleepy agricultural town to a dynamic suburban and commercial center. Today, it strikes a rare balance—combining small-town charm with big-city access, making it a magnet for families, professionals, and entrepreneurs alike. Location Situated just 16 miles east of Oakland and about 25 miles from San Francisco, Walnut Creek benefits from prime access to the greater Bay Area. The city is served by two BART (Bay Area Rapid Transit) stations, connecting it efficiently to surrounding urban centers. With convenient freeway access (including Interstate 680 and Highway 24), Walnut Creek offers both accessibility and seclusion—an ideal setting for both residential tranquility and business activity. A Thriving Commercial Scene Walnut Creek’s downtown is a beacon for shopping, dining, and culture. From high-end boutiques to popular national retailers, the area is often referred to as the “Rodeo Drive of the East Bay.” Beyond retail, the city is also home to a growing number of medical offices, law firms, tech startups, and financial institutions. The business landscape is increasingly diversified, thanks in part to the city’s favorable commercial development policies and strategic economic planning. With several new mixed-use developments and office parks underway, the demand for reliable commercial construction services, including expert concrete foundation work, is at an all-time high. B. The Role Of Commercial Concrete Foundations In Construction The Bedrock Of Every Building Whether you’re building a new office tower, warehouse, hospital, or retail center, every commercial structure starts with one thing: a solid foundation. Concrete foundations provide the structural integrity that ensures the longevity and safety of a building. They bear the weight of the structure, resist environmental stress, and provide insulation from soil moisture and temperature extremes. Types Of Concrete Foundations Common In Walnut Creek Given the region’s unique topography and seismic considerations, commercial projects in Walnut Creek must be built with foundations that meet specific structural and safety requirements. Common types include: In earthquake-prone areas like Northern California, foundations must also be reinforced with rebar and designed to flex and absorb seismic shocks. C. What To Expect From A Commercial Concrete Foundations Contractor In Walnut Creek 1. Site Evaluation And Soil Analysis Any experienced commercial concrete contractor, such as Spaulding Concrete, begins with an in-depth site evaluation. Soil quality, moisture content, slope, and compaction levels must be assessed to determine the best foundation type. In Walnut Creek, the presence of clay-heavy soil in some areas and hilly terrain near Mt. Diablo can complicate foundation work. A local contractor like Spaulding Concrete will have experience dealing with these specific conditions and will often partner with geotechnical engineers to perform comprehensive soil testing. 2. Project Planning And Permitting Permitting in Contra Costa County can be complex. Spaulding Concrete is familiar with Walnut Creek’s local building codes, zoning regulations, and permit acquisition processes. Expect us to: As a reputable contractor, Spaulding Concrete streamlines this bureaucratic process, saving you time and potential fines. 3. Excavation And Site Preparation Before pouring any concrete, the site must be excavated and prepped. This phase includes: Proper site prep is crucial—it determines how well the concrete will settle and cure. Mistakes here can lead to future issues like foundation cracks, water intrusion, or uneven settling. 4. Concrete Pouring And Curing Once everything is prepped, the actual concrete work begins. Spaulding Concrete uses high-strength concrete mixes designed for heavy loads and environmental resistance. Depending on the scale of the project, this might involve: The curing process is just as important as the pour. Spaulding Concrete monitors moisture levels and temperature to ensure proper curing, which typically takes 28 days for full strength. 5. Post-Pour Inspections And Testing Expect thorough quality assurance at this stage. Spaulding Concrete conducts: D. Key Qualities To Look For In A Contractor Choosing a commercial concrete foundation contractor isn’t just about price—it’s about partnership. Here’s what to look for when hiring in Walnut Creek: 1. Local Experience Experience in the Bay Area means familiarity with seismic standards, weather patterns, and soil types. A local contractor is more likely to have established relationships with city inspectors and suppliers. 2. Licensing And Insurance Ensure your contractor holds a valid California contractor’s license (typically a C-8 license for concrete) and carries liability and workers’ comp insurance. 3. Portfolio Of Past Work Ask for references and case studies. Review past projects similar to yours—especially those in Walnut Creek or nearby communities like Concord, Lafayette, or Pleasant Hill. 4. Technology And Equipment Look for contractors who use modern equipment (laser screeds, GPS-enabled grading, concrete pumps) and software for project management and progress tracking. 5. Communication And Professionalism You’ll be working closely with this contractor. Choose someone responsive, transparent, and willing to collaborate. Why Visit Walnut Creek? Top 3 Points Of Interest In Walnut Creek, California Nestled in the heart of the East Bay, Walnut
Are You Ignoring These Painful (And Costly) Commercial Signs Of Concrete Foundation Damage?
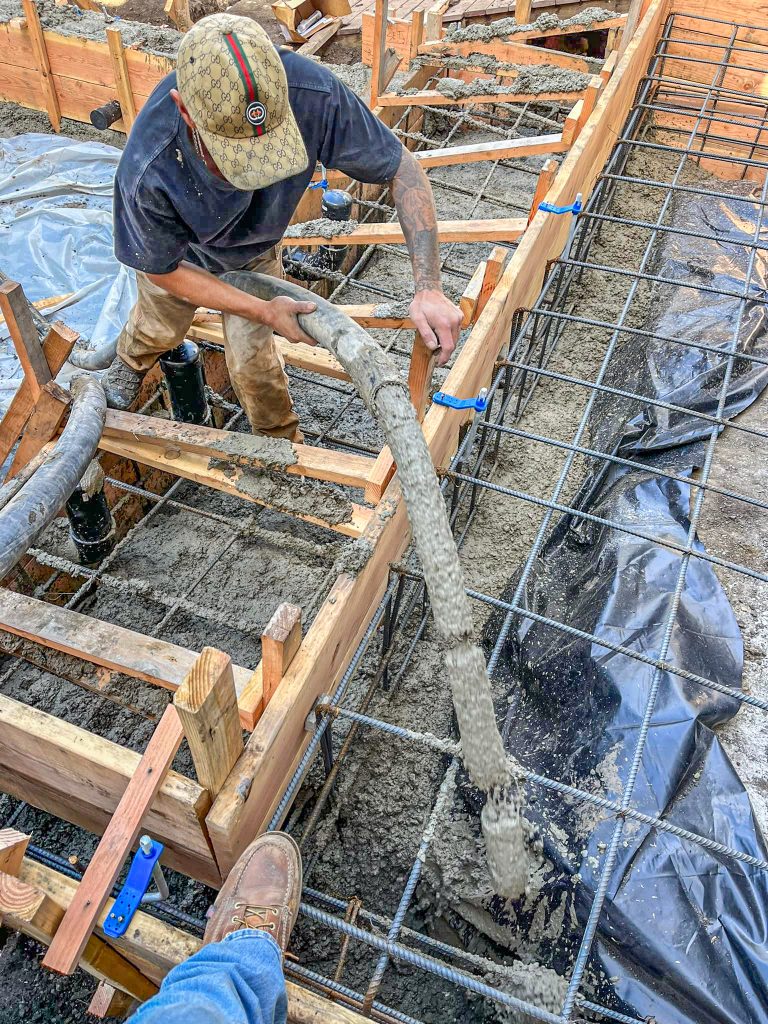
Are You Ignoring These Painful (And Costly) Commercial Signs Of Concrete Foundation Damage? Key Takeaways Regularly inspect your commercial foundation for early warning signs like cracks, uneven floors, or sticking doors to prevent small issues from escalating. Take care to keep soil conditions in check and drainage systems clear. Watch landscaping, environmental, and site factors that can contribute greatly to foundation damage. Have a professional regularly examine your foundation. Take advantage of new diagnostic technologies to identify concealed or emerging foundation issues early on and avoid costly repairs down the road. Repairing foundations as soon as possible is key! Failure to make necessary repairs can result in more expensive repairs, diminished property value, and safety or liability risks. Protect your foundation’s physical integrity with these preventative maintenance measures. Make priority improvements to drainage, gutter cleaning, and tree root management. Choose repair procedures that provide the greatest cost/performance benefit. Afterwards, get the experts involved to ensure that the fix is what your commercial property requires. Overlooking the warning signs of commercial concrete foundation damage can lead to expensive consequences. Cracks in walls, uneven flooring, and doors that no longer close properly are common red flags, especially in industrial and commercial structures. If ignored, these issues can escalate into major repairs. Water stains, shifting tiles, and visible gaps between walls and ceilings often point to underlying foundation problems that demand prompt action. Staying alert to these signs not only safeguards building occupants but also helps prevent unnecessary repair costs. Early detection allows for quicker, more affordable solutions, offering peace of mind and long-term savings. The following sections outline the most common warning signs, how to identify them, and the essential steps to protect your property from costly damage. Key Signs Of Foundation Damage Catching these early signs of foundation damage prevents expensive repair bills and protects your home from dangerous foundation failure. Minor shifts in your structure can indicate more serious issues underneath the ground level. It certainly pays off to keep an eye out for these signs of foundation damage and respond quickly. By paying attention to cracks, gaps, or new sounds, you maintain your building’s value and make future repairs less daunting. Retain all notes and photos for your files. This is important later if you ever need to show a pro what’s changed. 1. Cracks Appearing Inside Or Out Cracks in walls or floors show up for a lot of reasons, but not all cracks mean trouble. Hairline cracks under 1/8 inch wide can show from normal settling and often get fixed with epoxy or foam. Once they’re wider—above 1/4 inch—they can point to serious shifts. If you see cracks getting longer or wider, that’s a red flag. Cracks in stair-step shapes or running through bricks call for a pro’s look. 2. Floors Becoming Uneven Or Sagging An increase in slope, dip, or creaking noise may indicate a shifting foundation. To see if the floor is slanting, use a carpenter’s level or a bubble. This is especially true in older buildings, which tend to have sagging floors. This problem can be caused by a saturated, expanding earth pressing up against the foundation. Quick repairs prevent trips and more serious issues. 3. Doors And Windows Start Sticking If your windows and doors are suddenly sticking, don’t just look for loose hinges or a swollen door frame. If that’s not the issue, uneven door frames or gaps can indicate movement in your foundation. Cracks larger than 1/4 inch around door or window frames should not be overlooked. 4. Gaps Forming Near Walls/Floors Floor-to-wall or ceiling-to-wall gaps are usually a sign of movement. Measure how your house isn’t shifting. If they are larger than 1/4 inch and up to 1/2 inch, it’s time to consult a professional structural engineer. 5. Walls Begin Bowing Or Tilting Walls that lean, bow, or bulge can result from expansive soils or inadequate water drainage. If you notice nail heads popping out of your drywall repeatedly, it’s time to call in a professional to take a look. Bowing walls endanger the entire structure and require immediate action. 6. Chimneys Leaning Or Cracking Noticeably A leaning or cracking chimney, especially at the base, usually means there has been a shift in the foundation underneath. If you notice new cracks or a noticeable tilt, this needs to be examined immediately to prevent additional damage. 7. Utility Line Damage Clues Plumbing, gas, or electrical leaks often indicate foundation shifting. If you notice new leaks in your home or a sudden increase in your water bill, look for cracked pipes around the bottom. 8. Increased Moisture Or Mold Growth Wet basements or crawl spaces and a moldy smell indicate water is entering, usually due to inadequate drainage around the foundation or cracks in the foundation itself. Mold spreads quickly, so maintaining a humidity level below 60% will avoid damaging the foundation. 9. Exterior Walls Separating Slightly Keep an eye out for cracks between exterior walls and the soil or concrete patios. No matter how minor the foundation cracks might seem, ignoring them will only allow the damage to worsen. Document these changes by making notes and keeping a photographic record. 10. Subtle Sinking Or Shifting Sensations If you notice your floors creaking, shifting, or falling when you step on them, pay attention. That feeling, first experienced, can be a sign of soil movement under your property. This is especially true in clay or black soils, like those found in states such as Texas. Detecting Hidden Foundation Issues A reliable inspection goes beyond a walkable, cursory check. Identifying hidden foundation issues requires more than just examining walls and floors. An accurate inspection digs deeper, using advanced equipment and expertise to detect problems that aren’t visible to the unaided eye. Persistent puddles near the base of a building, for example, indicate poor drainage and can serve as early warning signs before cracks appear. In the Lone Star State, slab foundations are the most common type of residential foundation. Rapid soil swelling from
How Do Commercial Concrete Foundations Save You Thousands in Repairs?
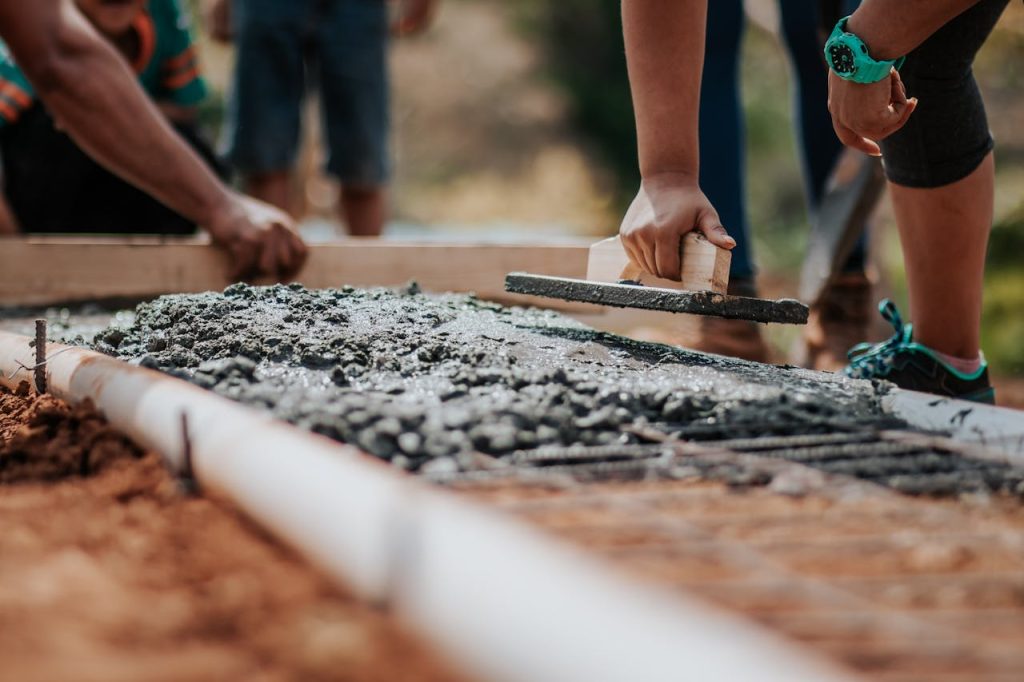
How Do Commercial Concrete Foundations Save You Thousands in Repairs? Key Takeaways Investing in commercial concrete foundations upfront helps prevent expensive repairs by providing strong support and long-lasting durability for large buildings. Opting for premium materials and superior construction methods minimizes the likelihood of cracking, shifting, and water intrusion in the future. Advanced planning, such as complete site evaluations and soil tests, makes sure the foundation is prepared for the requirements of the building and the environment where it’s built. Regular maintenance, including periodic inspections and ensuring drainage is functioning properly, will address small problems before they turn serious, saving you thousands in repairs, while preserving your property’s value. By including solid design elements and using steel reinforcements, the integrity of your foundation will be solidified. Furthermore, regular quality control helps increase resilience to soil movements and climate factors. See what to expect from emerging technologies like self-healing concrete and monitoring detection sensors. With proper implementation, these innovations will greatly increase the longevity of your commercial foundation and save you thousands in future repairs. A strong commercial concrete foundation does more than hold up your building—it protects your investment. By standing up to harsh weather, soil shifts, and everyday stress, a well-built foundation helps prevent the cracks, leaks, and structural issues that lead to costly repairs. That means fewer patch jobs, less downtime, and more money saved over the long haul. In regions with heavy rain or intense heat, quality concrete work offers consistent protection, keeping walls straight, floors level, and water out. The result? Long-term value, lower maintenance costs, and fewer emergency calls to the repair crew. In this post, we’ll explore exactly how the right foundation choice can lead to thousands in savings—and share a practical checklist to guide you before your next project begins. What Are Commercial Concrete Foundations? Commercial concrete foundations create the foundation for any large commercial building that provides a solid structure and long-term durability. These commercial concrete foundations ensure heavy loads are properly supported and prevent buildings from subsiding or moving. They help to make sure the building stays strong for many decades to come. For public safety, this must remain true even when the earth moves or the storms rage. They do one cool thing—distribute the load of the structure so that all the stuff above stays level and sound. With thousands of projects done across Southern California and Arizona, we have seen that the right foundation is key to avoiding big repairs down the line. Defining Scale And Purpose One major difference is that commercial concrete foundations are substantially larger compared to residential foundations. Where a house might use a simple slab or crawl space, a big office or warehouse might need deep piers or thick mat slabs. These are some of the deepest foundations, sometimes going several dozen feet below ground to reach still soil. Some have to support several thousand square feet, or even support tilt-up walls and parking decks. On every project, the engineers analyze the requirements of the building and the native soil conditions. They select the preferred foundation type, ranging from shallow footings close to the surface to deep piers constructed with galvanized steel. Certain piers can support 74,000 lbs, providing genuine support for stout commercial structures. Key Differences From Residential Constructing a commercial foundation requires tougher materials and tougher requirements than residential structures. Just to name a few, designs typically call for thicker slabs, more steel rebar, and deeper footings. These foundations are deeper and heavier since commercial buildings have more weight to support. In addition to that, they need much higher safety standards. Why Concrete Is The Standard Concrete endures far longer and requires minimal maintenance. It continues to perform through extreme weather and can be customized to accommodate any building façade. This combination provides excellent versatility, making it an excellent option for all types of commercial jobs. How Quality Foundations Slash Repair Bills The long-term value of a quality commercial concrete foundation saves you money and trouble, assuring that your home is well-built. By preventing cracks, settling, and water infiltration before they begin, you save on major repair costs. By employing the proper materials and intelligent design, you’re not just saving costs—you’re protecting your property. When you work with an experienced contractor, you get work done right the first time, which helps you avoid costly mistakes. 1. Superior Load Distribution Prevents Settling A well-built foundation distributes the load of the structure down through the earth. This prevents unbalanced settlement, where one side sinks or cracks. When you use engineered slabs and extend your footings deep into stable substrata, you achieve much more consistent support. Such construction methods, like using drilled piers ahead of construction to prevent soil from moving below your feet, save millions in repair costs. 2. High-Grade Materials Minimize Cracking Choosing quality concrete and steel helps avoid cracks in your foundation before they start. Even though materials may range from $500 to $5,000, making the right selection will reduce the risk of extensive and costly repairs in the future. Avoiding air entrapment in good quality control during mixing and pouring helps to ensure that the slab remains tight for decades. 3. Effective Water Management Stops Damage Quality drainage systems, such as French drains or sump pumps, immediately take water away from your foundation. High-quality grading and waterproofing can make your home resilient, easily shedding heavy rain without letting moisture into your foundation. These measures dramatically reduce the chances of cracks and/or mold. 4. Robust Design Withstands Soil Shifts Clay soils incredibly swell with rainwater and shrink in drought, creating a 5% to 10% expansion of the volume. Careful foundation design, combined with thorough geotechnical testing, ensures that your slab remains stable even when the ground shifts. 5. Proper Curing Boosts Long-Term Strength Allowing important concrete to cure is an essential factor. If this step is neglected, the rebar becomes the source of weak points. With experienced laborers laying the foundation, there’s no substitute for quality craftsmanship to create a
Is Your Commercial Building In Walnut Creek At Risk Because Of Poor Concrete Foundations?
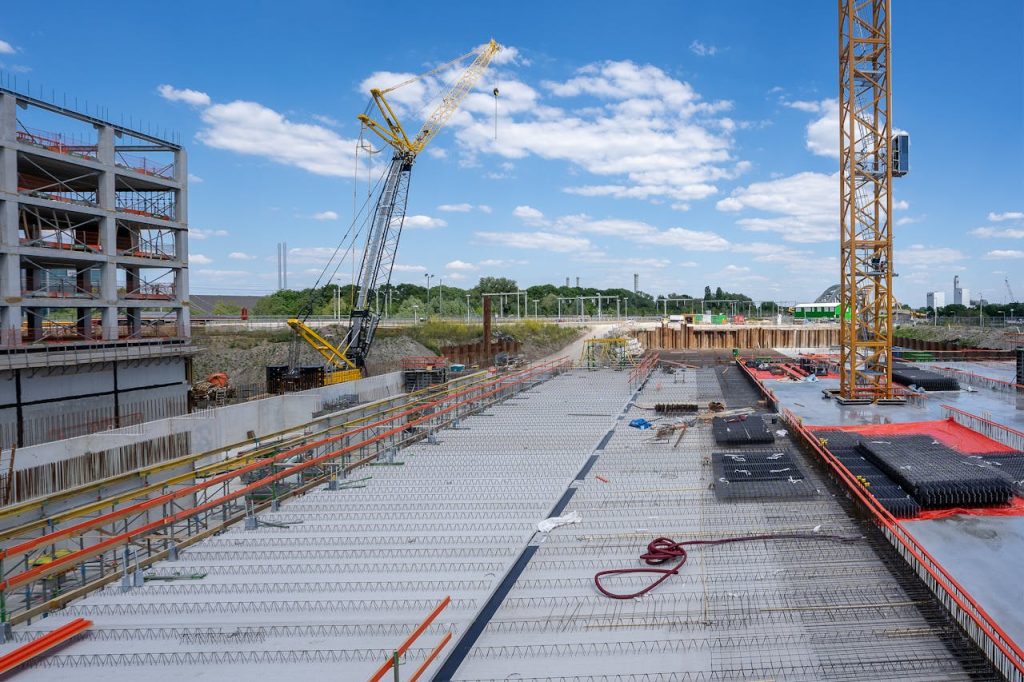
Is Your Commercial Building In Walnut Creek At Risk Because Of Poor Concrete Foundations? Key Takeaways Regularly inspect your commercial building’s foundation for visible cracks, uneven floors, and sticking doors or windows, as these are early warning signs of distress. Prioritize foundation repairs that address Walnut Creek’s specific soil conditions, local climate, and seismic zone needs. This will protect the buildings and provide a stable environment for many years to come. Ensure adherence to local building codes and obtain any required permits. Prevent costly violations and maintain commercial safety with mandatory inspections. Avoid costly future repairs due to poor foundation conditions by taking action before damage spreads with our expert diagnostic tools and foundation repair processes. Always involve an experienced geotechnical engineer when making repairs or planning new construction. Their collective experience will give you the tools to better design safer and longer-lasting foundations. Avoid increased exposure with detailed documentation, long-term monitoring, and maintenance plans to save property value, reduce liability, and help preserve business continuity. A compromised concrete foundation can put any commercial building in Walnut Creek at serious risk. Cracks, sagging floors, stuck doors, and water intrusion are more than just inconveniences—they’re early warning signs of deeper structural issues that can disrupt your business and lead to costly repairs. Problems like shifting soil and poor drainage often get worse over time, quietly shortening the lifespan of your building. And while Walnut Creek’s building codes outline what a safe foundation should look like, many older structures fall short of today’s standards. That’s why proactive maintenance—like regular inspections and timely concrete repairs—is key. In this article, we’ll walk through how to spot foundation problems early and what you can do to keep your property safe and fully operational. What Defines Poor Concrete Foundations? A good concrete foundation is essential to the success of your commercial building for many years to come. When concrete foundations don’t hit the mark, tangible issues can begin to surface. While cracks in the floor might be the worst manifestation of bad concrete work in Walnut Creek, they’re far from the only concern. For too many people, that results in expensive repairs, lost time, and even life-threatening situations. There are various contributing factors for these problems, and each factor should be carefully examined to ensure your structure remains safe for decades. Inferior Concrete Mix Issues Maximizing our use of low-grade cement or sand reduces the concrete’s initial strength. It cures improperly if the mix retains excess water or an incorrect cement-to-sand ratio. That can range from just hairline cracks developing to crumbling concrete at the edges. A warehouse floor can begin to show damage simply from having forklifts make their daily rounds. Moisture will gradually make its way into these cracks. This rusts the steel inside and causes it to expand and further crack the slab. Inadequate Design For Load Foundations must distribute the weight of your structure. If this step is hurried or overlooked, the entire foundation can buckle. If calculations overlook loading from large equipment or storage racks, the concrete foundation may end up settling in different areas. This results in sloped floors or misaligned doors, which can worsen with every passing year that goes by. Construction Errors And Shortcuts Skipping rebar, pouring too quickly, or failing to let the slab cure properly are frequent mistakes. These measures may seem like they save time in the short run, but they result in hollow patches or soft spots. If you’re looking for an obvious indicator, you may be able to spot sunken sidewalks or gaps beneath your exterior walls. Ignoring Local Soil Conditions Soil in Walnut Creek goes from heavy clay to sand. Not testing it before building means you may not know if it will shift or pull away from the slab. This can create an imbalance by pulling the entire foundation down to one side, resulting in cracks or doors that stick. What Dangers Lurk Below? A deteriorating concrete foundation can hold much more serious implications than just a few cracks in the walls. So, if you operate or own a commercial property in Walnut Creek, you should be on high alert. These small dangers under your feet can turn into big, nasty surprises down the road. Here’s how things can fall apart and why these nonsensical problems deserve your focus. 1. Compromised Structural Integrity Risk A wobbly base endangers the entire structure. When that base shifts or crumbles, beams and columns above begin to shift right along with them. In the long run, this can weaken the entire structure. If you have a manufacturing facility, that equates to life and safety hazards for all who have business or pleasure within. 2. Uneven Building Settlement Issues Soil changes or bad construction could cause portions of the structure to sink or lean. You could encounter warped floors or sticky doors that no longer latch properly. This type of settling only gets worse, putting ever-increasing stress on each building element. 3. Significant Wall And Floor Cracking Bowing walls, large cracks in walls or floor slabs typically indicate the foundation is failing. These gaps allow massive amounts of water, air, and at times even rodents and insects, into the building envelope. As they expand, these fissures further exacerbate and eat away at the structure’s skeleton. 4. Persistent Door And Window Jams If doors or windows jam, the frames can be misaligned from a shifting foundation. This not only complicates everyday work but can even leave people stranded at home in an emergency. 5. Potential Plumbing System Damage Drains, electrical systems, and hydraulic pipes and equipment run underneath the concrete and subsoil. When these pipes shift under the weight of bending or breaking foundations, leaks and water damage are inevitable. Along with huge repair bills, this can lead to significant disruptions in operations. 6. Increased Moisture And Mold Problems Once these structural cracks and movement occur, they allow water to enter, saturating carpets, drywall, and other furnishings. Mold grows quickly in damp areas and can
What’s The Real Difference Between Residential And Commercial Concrete Foundations?
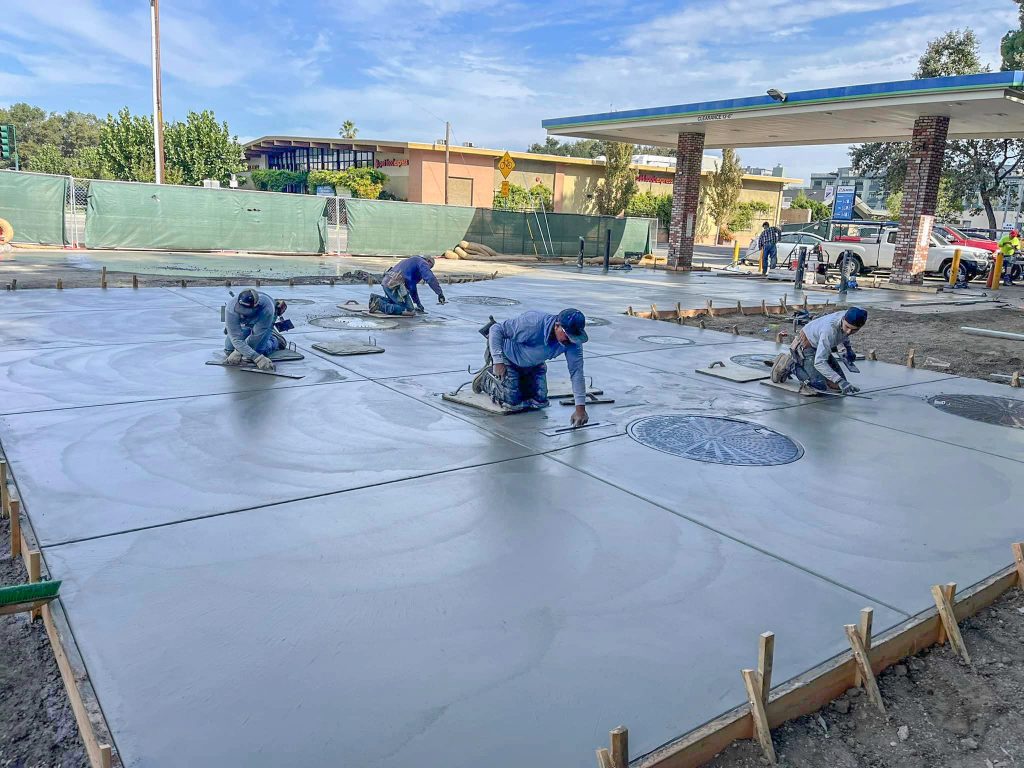
What’s The Real Difference Between Residential And Commercial Concrete Foundations? Key Takeaways Knowing the major differences between residential and commercial concrete foundations can ensure you choose the right option for your new building project. Residential foundations usually require simpler designs and less material due to lighter structures, while commercial foundations need to support heavier loads and complex designs. Don’t skimp on foundation type considerations. Pay attention to soil conditions, load requirements, and building codes to make sure that the foundation will provide long-term stability and safety. That’s why site prep and soil analysis are so important. Through focused quality control, they protect against expensive damage and increase the longevity of your foundation. Budgeting and timelines differ drastically. Be sure to budget for things like materials, labor, permits, and other unforeseen costs that could pop up. Concrete foundations, residential or commercial, should be regularly inspected and maintained. They are key to early detection of problems and to helping you keep your foundation’s structural integrity for years to come. What’s the real difference between residential and commercial concrete foundations? After working with both on various projects, two key factors stand out: size and load capacity. Residential foundations typically support the lighter loads of homes, while commercial foundations are designed to handle much heavier weights from large buildings or industrial equipment. Commercial projects often involve thicker slabs, deeper footings, and more steel reinforcement. Additionally, code requirements are much stricter for commercial work. In residential construction, standard rebar and basic grading are often sufficient. However, for commercial buildings like stores or warehouses, custom mixes and stricter regulations are usually the norm. Regardless of the project type, both residential and commercial foundations require careful planning and skilled craftsmanship. There’s no one-size-fits-all approach—I tailor each project to meet its unique needs. Explore more details in the sections below. What Are Residential Foundations? A residential foundation is the large base that supports a house or other small structure. Doing this distributes the weight of the house evenly across the foundation so the house can sit correctly on the soil. Almost all residential structures require a solid foundation to remain even and secure. If a foundation settles correctly, the structure can remain healthy for many generations. Without a firm foundation, even routine changes in the soil or the weather will lead to cracks or movement. One in ten homes in the U.S. faces residential foundation damage. That’s why this hidden realm of construction is so desperately important. Defining Typical Home Structures Most homes, from bungalows to ranch houses to two-story homes, take advantage of residential foundations. Since these buildings don’t have the same load as commercial buildings, their base doesn’t need to be as fortified. The exterior appearance of a residential structure, as well as its height, can make a difference in what foundation is most appropriate. A two-story house will require a wider or deeper foundation than a one-story house might. Choosing the best foundation for residential buildings requires an understanding of the type of building and how much load it will bear. Common Residential Foundation Types You’ll find slab, crawl space, and basement foundations in residential construction. A slab is a concrete pad typically 6 to 8 inches thick. It is quick to install and performs very well in hot climates. Crawl space foundations lift the home several feet, allowing you to access pipes, wires, or ductwork. Basement foundations dig even lower, providing room for storage or additional living spaces. Each one has advantages and disadvantages. Slab foundations can provide an affordable option with low maintenance. Conversely, while basements afford more living space, they entail a significant premium and increased time to build. Factors that guide the choice: Soil type Local weather House design Budget Need for storage or access Why Simpler Designs Often Suffice Residential buildings don’t require complicated foundations like large commercial office towers do. Flimsier walls and roofs require less material, labor, and factory time. Considering that most homeowners have cost concerns, an easy base, such as a slab or a crawl space, suffices. Easier maintenance, fewer components, and a more straightforward approach allow for simpler repairs and inspections. Regularly inspecting for cracks, leaks, or shifting prevents larger issues from developing. What Are Commercial Foundations? Commercial foundations are the baseline for larger, more complex structures. These are the literal support systems for places as diverse as high-rise office towers, suburban malls, industrial warehouses, and urban hospitals. You find these foundations at the heart of buildings that see high foot traffic, hold heavy machines, or need multiple stories. The key design and performance objectives are deep lateral support, long service life, and resistance to harsh environmental and soil conditions. Understanding Larger Building Needs Heavy structures such as commercial offices or retail establishments require a foundation that is both capable of supporting additional loads and the load to rise. Unlike residential foundations, commercial foundations often extend much further into underlying less active soil layers, promoting greater overall stability. When a structure occupies a large footprint, the base it stands on needs to widen in order to support it all without tipping, rotating, or bending. Heavier loads require a stronger and thicker foundation. For example, a hospital with heavy medical gear or a shopping mall with several floors needs deeper footings and a thicker slab than a small home. Projects on commercial foundations in clay country need special considerations. This type of expansive clay soil can cause foundation damage as it expands when wet. Common Commercial Foundation Approaches Typical options, especially for urban or developing areas, include slab-on-grade, mat foundations, and pile foundations. Slab-on-grade is the preferred foundation, being cheaper and easily repairable with methods such as polyjacking when necessary. Mat foundations are effective at spreading out very heavy loads. Piles reach down deep into the earth for additional support. Even before any above-ground construction occurs, they install drilled piers or footings, often going down to rock. When picking a type, you look at: Soil type and stability Weight of the building Lifespan needed