What Should You Ask a Contractor Before Hiring Them for Stamped Concrete Work?
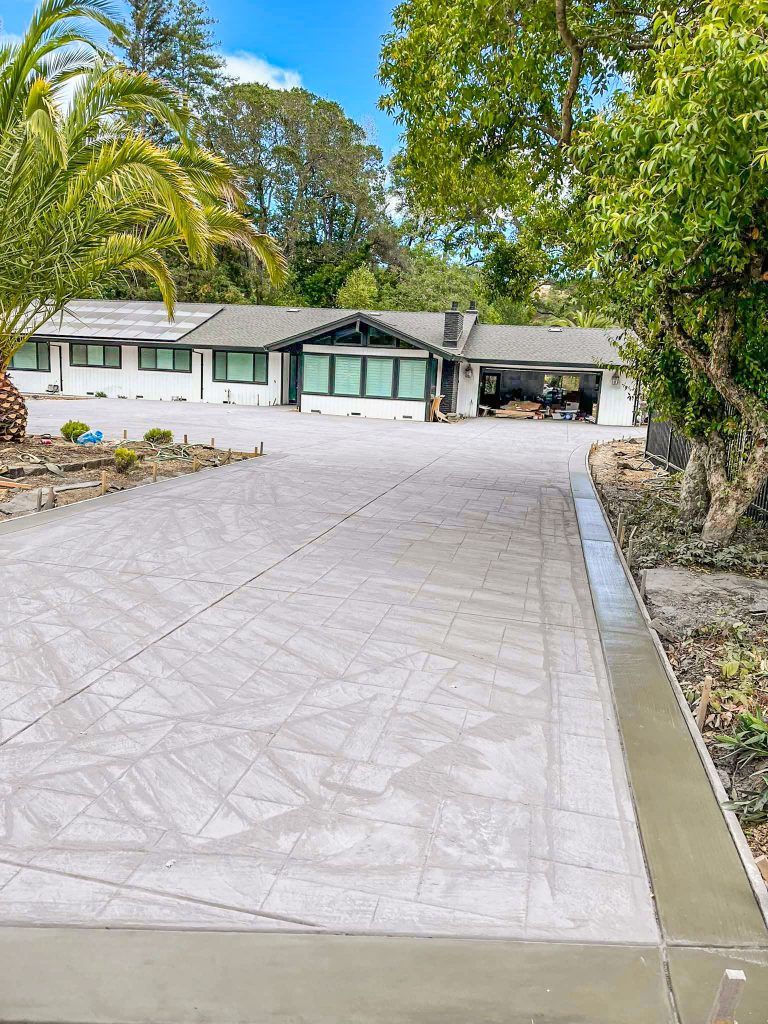
What Are The Biggest Mistakes People Make When Building Residential Retaining Walls? The key to hiring the best installer or contractor to work with stamped concrete is to ask the right questions about their experience, portfolio and references. Make sure they have experience with projects like yours and can provide photographs of their completed work. Inquire about how they plan to approach your specific project, what types of stains or mats they’ll use, how they will address site preparation and curing, etc. Knowing their anticipated timeline and if they have a warranty will make sure expectations are set from the beginning. Make sure to go through costs carefully, and be clear about what may be considered extra. Asking these questions will help you better gauge their experience and work ethic, so you can choose the right contractor for the job. Here, we’ll outline important issues to discuss when speaking with a contractor for your stamped concrete. Key Takeaways Be sure to check a contractor’s credentials—including licenses, insurance, and any relevant certifications—to ensure they’re in compliance with local regulations and the best practices of the industry. This ensures your investment is safeguarded, and the risk of future problems is reduced. Question them directly on how many stamped concrete projects they’ve done. Ask for samples of their previous work to ensure they have the experience to handle the design you want and factor in your local climate conditions. Ask the contractor how they plan to get the required permits. This will assist with a smooth execution, avoiding any potential legal or scheduling conflicts. Request a detailed written estimate, clarify the payment schedule, and understand warranty terms to avoid misunderstandings and protect your financial interests. Establish clear communication methods and identify a main point of contact to stay informed and address any concerns during the project. Don’t ignore these warning signs! If they give vague answers, use high-pressure sales tactics, or turn in an unusually low bid, that’s a good indication you can’t rely on them. Why Contractor Credentials Matter Most When hiring a contractor to do stamped concrete work, credentials are about the best indicator there is of professionalism, skill level, and commitment to the craft out there. They help keep your investment safe, while minimizing the risks associated with shoddy work or legal issues. A contractor’s credentials are not just boxes to check but rather proof of their status and commitment to providing the best possible outcome. Protecting Your Investment Seriously With the right licenses and certifications, a contractor will protect your financial interests. Only licensed contractors are required to abide by rigorous standards. This common sense requirement protects us from shoddy work that results in costly fixes. When your contractor is certified by the American Concrete Institute (ACI), you know you’re getting a project built to last. They will ensure that the strength requirements are maintained. This is particularly important for small jobs in projects such as driveways where ACI-certified contractors finish 95% of projects on schedule. Adequate insurance coverage is hands down the second most important aspect. A contractor who has liability and workers’ compensation insurance will relieve you of any surprise project-related expenses should an accident happen while work is being performed. If you don’t ask for this, you may find yourself financially liable for any damages or injury. Avoiding Costly Legal Nightmares Both federal and local requirements credentials can help you comply with local regulations, which can save you a fight—or a fine. Proper licenses prove a contractor knows and follows permitting procedures, a key for ongoing property care for years to come. For instance, a mangled project had the correct permits and approvals been pursued, might result in issues when you eventually decide to sell your property. Experienced contractors, especially those who have been in the industry for decades, bring a wealth of understanding that can minimize costly errors. A company with a stellar reputation—confirmed through third-party sites like the Better Business Bureau—seals the deal on their trustworthiness. Ensuring Project Quality Standards Credentials demonstrate a contractor’s dedication to quality. Certifications—including American Concrete Institute (ACI) certifications—demonstrate a commitment to advanced training and mastery of state-of-the-art industry best practices. Only a certified contractor can deliver precision, defect-free, and durable stamped concrete artistry. This is true for everything from the most residential patios to massive commercial parking lots. Key Questions About Credentials So when engaging a contractor to perform stamped concrete work, knowing their credentials is key to making sure you’ll get quality, compliance and professionalism. Here are the key areas to consider when judging their credentials. Verify Current Licensing Status Begin with requesting evidence of a current contractor license. Make sure that it’s current and released for your state or locality, as this serves as verification that they are compliant with legal mandates. A properly licensed contractor shows that they are serious professionals and accountable businesspersons. Inquire about prior disciplinary actions and rule violations. For instance, a contractor with a good record will be less prolific in violating regulations and providing unreliable service. Looking them up on the Better Business Bureau can uncover more information about their trustworthiness as well. Confirm Adequate Insurance Coverage Ask them to provide proof of liability and/or builder’s risk insurance policies to cover accidents that occur on-site. This shields you from surprise costs as the project progresses. Ensure that your contractor has workers’ compensation insurance that covers their employees. Without proper insurance, you may expose yourself to considerable financial and legal liability, particularly if anyone is injured. Make sure that those policies are up to date and relevant to the project. Check for Specific Certifications Ask about certifications. For example, American Concrete Institute (ACI) accreditation shows subject matter mastery when it comes to concrete work. Relatedly, certifications can draw attention to a contractor’s pursuit of quality, such as ISO certification or LEED accreditation. For stamped concrete projects, ACI certification can be the difference between success and failure. It shows evidence of specialized training and adherence to the industry’s best practices. Inquire About
What Are the Most Common Mistakes People Make With Stamped Concrete?
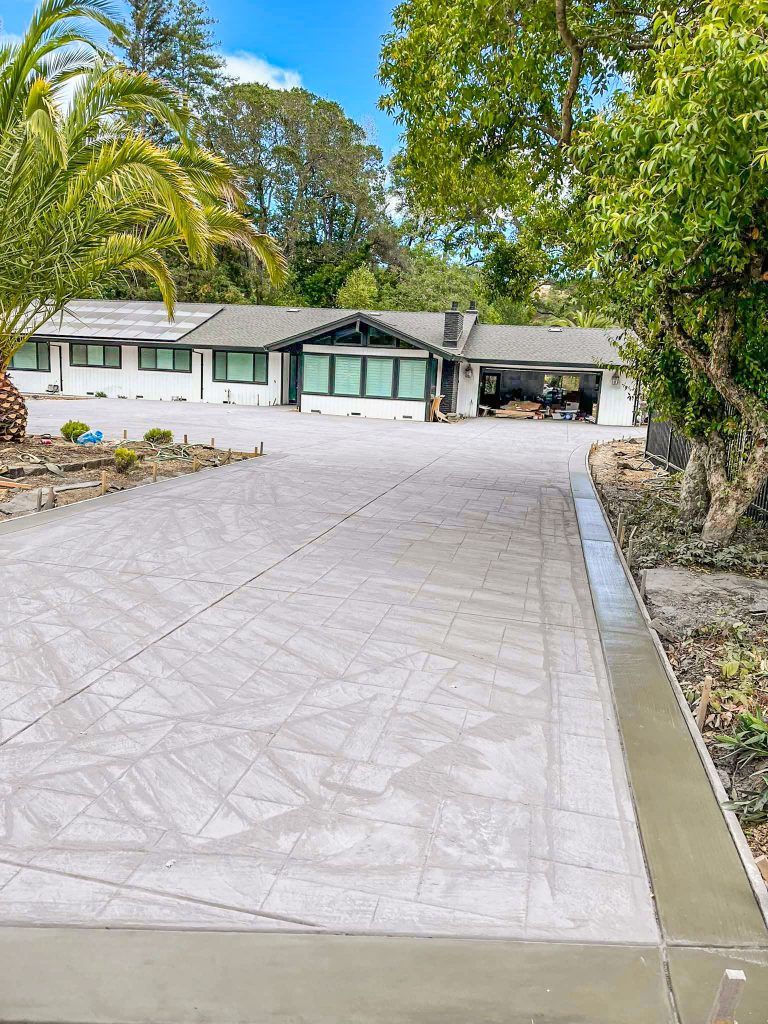
What Are The Biggest Mistakes People Make When Building Residential Retaining Walls? The wrong installations, maintenance or design decisions lead to almost every mistake made with stamped concrete. One of the most common mistakes is neglecting to prepare the base properly, which can cause uneven surfaces or cracking over time. Skipping a quality sealer or neglecting to reapply it as scheduled will immediately negate this durability. This lack of care leaves the surface vulnerable to staining and fading. Selecting stamp patterns or colors that don’t pair well with other architectural elements on the property may leave you with a jarring appearance that hurts your curb appeal. The failure to clean routinely can make dirt accumulation start to wear on its look. Knowing about these mistakes is the first step to ensuring the longest life and most beautiful look for your stamped concrete. In just a few short pages, we’ll get into detailed suggestions for preventing all of these problems. Key Takeaways Choosing the wrong pattern or color combination is just as important as the cost of raw materials. Don’t skip on grading, compacting the sub-base and reinforcing the slab, or you’ll have a recipe for cracking and instability. Select superior concrete mixes and ensure that they are consistently applied to achieve a lasting, beautiful finished product. Don’t skimp on quality concrete or if incorrectly mixed it can cause aesthetic and structural problems. Avoid installing under extreme weather considerations, whether it is hot or cold, rain or snow. Place concrete on ideal temperature days and avoid extreme heat, cold and rainy days for the best success. Apply release agents and sealers according to manufacturer instructions to protect the surface and bring out its best look. Neglecting to seal or sealing incorrectly can result in premature wear, discoloration, and stains in your concrete. Make sure stamps are aligned properly and don’t skip steps in the stamping process. Proper installation avoids the appearance of misaligned patterns or uneven textures, showing a professional touch. Maintain your stamped concrete by regularly cleaning and resealing it. Failing to address minor issues leads to expensive fixes and a lackluster look as the years go by. Common Stamped Concrete Mistakes Whether you’re a DIY stamped concrete enthusiast or a veteran contractor, there are some common stamped concrete mistakes that plague everyone at some point in stampede. Most mistakes arise from a lack of planning or rushing the job resulting in expensive fixes or less-than-ideal outcomes. Knowing what to expect at each step in the stamping process is key to getting a finished product that’s both long-lasting and beautifully aesthetic. Skimping on Sub-Base Preparation Sub-base preparation is one of the most important aspects of creating a stable, long-lasting surface. Properly grading and compacting the sub-base keeps the stamped concrete slab from shifting or cracking in the years to come. For instance, failing to properly compact the base can lead to sinking and cracking, particularly noticeable on driveways or patios where level surfaces are essential. Use a checklist of crucial steps to take before pouring concrete. First, clear away debris, soil the ground, and add a slope with at least a 3/16-inch drop per foot to encourage proper drainage. Choosing the Wrong Concrete Mix Choosing a concrete mix specifically formulated for stamping use is essential. Durability wise, commercial stamped concrete mixes, minimum 4,000 PSI with 5–7% air entrainment are suggested. Mixes that are inexpensive or more generic tend to open up linear cracking and fail when placed under stress. Ignoring Proper Reinforcement and Thickness You steel reinforce concrete with steel rebar or wire mesh to prevent cracking. It’s vital to keep the correct thickness—usually 4 inches for patios and 5 inches for driveways—to provide structural support. Under or no reinforcement, even with a strong mix design, lack of reinforcement will accelerate failure. Speeding Through the Stamping Stamp alignment needs to be perfect. By sticking to a simple step-by-step method, you steer clear of splotchy or mismatched impressions. Hurrying will lead to bad texture, especially with stamped concrete. Misusing Release Agents Applying release agents evenly will help you avoid sticking and keep your surface texture intact. Mishandling can lead to ugly color changes or ugly spots. Disregarding Weather Conditions Extreme cold or heat can have a significant impact during the curing process. Too much early freezing causes weakening of concrete, sometimes up to 50%. Applying Color Inconsistently Uniform coloring techniques avoid patchy or mismatched areas. Sealing Inadequately Sealing it well is key to increasing its life span. Neglecting this important step means your concrete will be susceptible to stains, wear, and damage. Forgetting Expansion Joints Properly spaced joints allow movement, avoiding cracks. Neglecting Ongoing Maintenance Routine cleaning and resealing preserve appearance and durability. Design Flaws and Aesthetic Issues Producing high-quality stamped concrete takes an artist’s eye and an engineer’s detail-oriented approach to avoid design oversights that can drain its aesthetic allure. It can sometimes be made to resemble other materials, such as slate, brick, or wood, through stamped concrete. It won’t quite mimic their organic appearance, so plan design wisely. Poor planning or neglecting practical design principles often leads to surfaces that fail to complement their surroundings or meet expectations. Selecting Inappropriate Stamp Patterns A missed opportunity is often selecting pavement patterns that don’t fit within the context of the surrounding landscape or built environment. For example, a natural flagstone patio might not look appropriate against a contemporary house with lots of glass and steel finishes. Rather, it’s that patterns need to be appropriate to the style of the building. Traditional favorites such as cobblestone for a period feel or wood planks for a natural, warm appearance. Here’s a quick comparison for clarity: Stamp Pattern Suitable For Cobblestone Traditional patios Slate Pool decks Brick Walkways Mismatched designs, like mixing tactile designs with clean design elements, can produce a jarring aesthetic. Incorrect Stamp Alignment and Placement Misaligned stamps or inconsistent stamping placement is a second pitfall that pulls away from an otherwise beautiful finished look. Careful attention to alignment will go