How Do You Know If You’re Choosing The Wrong Type Of Commercial Concrete Foundation?
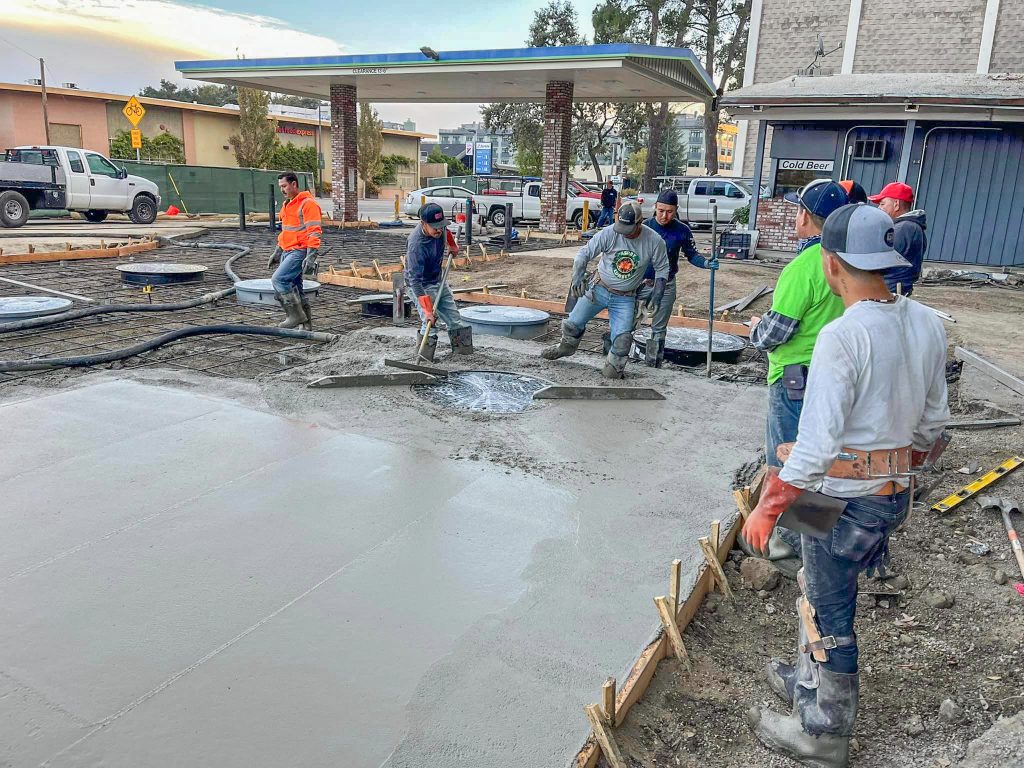
How Do You Know If You’re Choosing The Wrong Type Of Commercial Concrete Foundation? Key Takeaways How to know if the wrong type of commercial concrete foundation is being selected? The choice depends on the structure’s scale, ground conditions, and loading needs to maintain structural integrity. Regular monitoring for visible cracks, uneven settling, and moisture issues helps detect foundation problems early and prevent costly damage. Conducting thorough soil tests and understanding local building codes are critical steps before selecting a foundation type for any commercial project. Working side by side with foundation engineering experts and employing pre-construction site testing methods ensures costly construction phase missteps are avoided. Prioritizing long-term durability improves the ability to achieve a foundation that lasts. Planning for future maintenance helps avoid repeated costly repairs. Continuous learning about new foundation techniques and technologies enhances the efficiency, safety, and performance of construction projects. Choosing the wrong type of commercial concrete foundation shows up in signs like cracks in the floors, walls that start to bow, and doors that stick or won’t close right. Common issues include sagging cracks in interior floors, standing water along the edge of the building, or flaking delamination at the concrete cornice. These problems result from an incorrect choice of foundation type in relation to the soil or loading requirements of the site. Active pipe leaks or unusual noises coming from below serve as another major alarm. Over time, minor defects escalate into major renovation projects. This post breaks down the most common warning signs and shares what to check so issues can be spotted early, keeping the building safe and steady. What Are Commercial Concrete Foundations? They hold up all that weight and make sure everything stays nice and even. Concrete foundations are made entirely of concrete, a durable and resilient material that provides a firm foundation. Typically, they are much deeper than they are wide. Generally, their depth-to-width aspect ratio is greater than 4 to 5. Their arrangement typically consists of a slab on grade, commonly a 4 to 6-inch-thick concrete slab. This sturdy foundation allows the building to thrive for decades. With the proper type of foundation, heavy or light, the building will be safe, steady, and secure, regardless of the load above or the soil underneath. Defining Shallow Foundation Systems Shallow foundations are located near the ground surface, making them relatively inexpensive and easy to install. The two most typically used types are slab-on-grade and spread footings. Slab-on-grade slab foundations are a single slab, usually four to six inches thick, that sits directly on the ground. Spread footings would employ concrete pads to distribute the load across a larger surface. For light buildings, such as low-rise office spaces or small retail storefronts, builders usually opt for shallow foundations. Approximately 80% to 90% of all one- and two-story commercial buildings utilize this type of foundation. These systems allow for lower unit costs and a faster overall build. Exploring Deep Foundation Systems Deep foundations extend far down to stable soil or bedrock. Types of commercial concrete foundations include pile and drilled shaft foundations. While piles are generally long columns driven deep into the ground, drilled shafts are, as the name suggests, holes filled with concrete. Consider heavy structures such as skyscrapers or locations built on soft soil—all scenarios that require deep foundation support. Deep foundations take on larger loads and more problematic soil. Key Differences: Shallow VS. Deep Shallow foundations don’t reach as great a depth but are more appropriate for light loads and strong, stable soil. Deep foundations extend deep underground to reach sturdy base layers and support heavier loads. Shallow types are less expensive and can be constructed faster, but deep types are better for taller and heavier buildings. Signs You Chose The Wrong Foundation Identifying the wrong type of commercial concrete foundation from the start goes a long way in protecting your building’s longevity and structural integrity. You can read the signs as they happen in person. Cracking, leaking, and premature deterioration result when the foundation is wrong for the intended use. By paying careful attention to your foundation, you can identify small problems before they become large ones. 1. Visible Cracks And Settlement Issues Cracks in walls or floors make the list as the number one sign. These cracks may be caused by damage from extreme heat, plumbing leaks, tree roots, or when concrete dries too quickly. Vertical cracks typically indicate foundation settlement. Slab-on-grade footing cracks are never seen since the footing is below the ground and hidden. Any movement is quickly revealed through sloped floors or doors that stick. Swift action from an expert prevents more costly issues from accumulating over time. 2. Unexpected Moisture Or Water Problems When water comes creeping in, that’s a sign your drainage system has failed. All of that stuff is heavy rain, bad run-off, or the absence of waterproofing that allows moisture to come in. That undermines both the foundation and what it allows to stand above it. You need that waterproofing underneath yesterday if you start noticing moisture coming through or puddles forming. 3. Structure Performs Below Expectations A building that is sinking, wobbly, or moving around indicates the wrong foundation. If the concrete base doesn’t adequately compensate for the soil conditions or weight of the building, the entire system operates suboptimally. Having a keen eye on your foundation choice prevents issues from developing into roadblocks that hinder your progress. 4. Foundation Exceeds Maintenance Needs If it requires a lot of fixes—paving over, raising, filling in, and repairing—it indicates the design was probably the wrong appropriateness. Foundational foundations should make maintenance minimal. When maintenance is consistently forced to take the back seat, that’s something deserving of a more serious examination. 5. Early Material Degradation Observed If floors, beams, or other supports begin wearing prematurely, your foundation is likely misaligned. Salt, water, and weather exacerbate this process. Recognizing compromised components indicates it’s time to take a closer look at the foundation. 6. Mismatched Foundation And Soil Behavior Getting the
What Happens When You Skip Proper Concrete Foundation Prep In Commercial Projects?
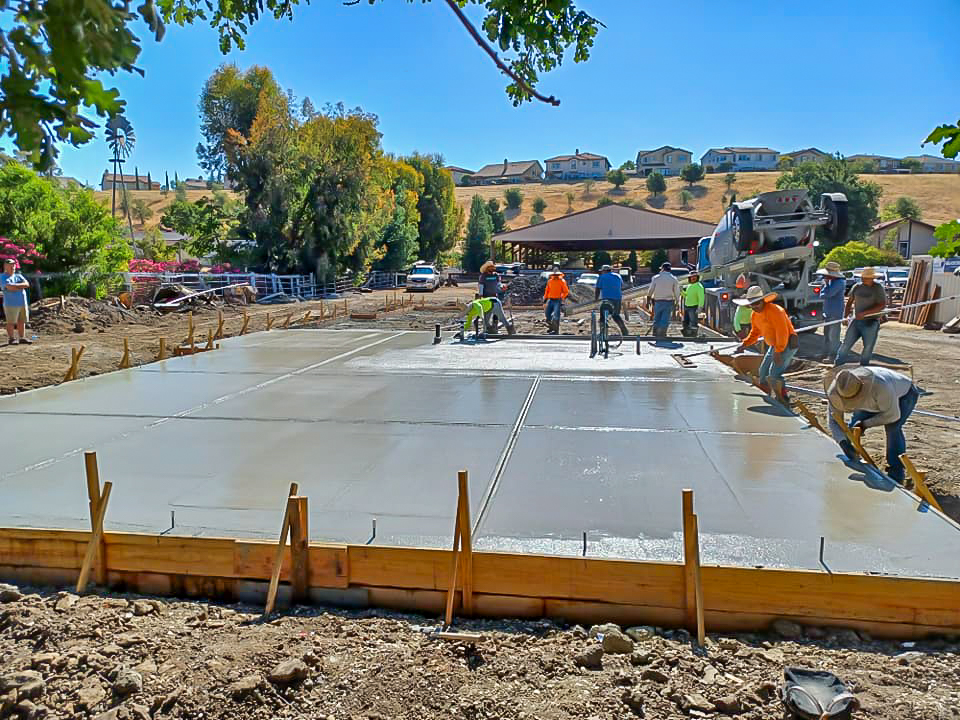
What Happens When You Skip Proper Concrete Foundation Prep In Commercial Projects? Key Takeaways Proper site preparation sets the stage for smooth, strong, and enduring commercial concrete foundations. It all begins with careful planning and making sure you have a clean and level surface. Evaluating ground conditions and soil testing will save your commercial project from skipping the proper foundation prep. These steps help make sure your plan is customized for the unique location. Providing proper grading and managing drainage are key to keeping water away from concrete. Just as importantly, these steps protect against erosion that can undermine a solid foundation over time. Building on the correct materials and proper soil compaction protects your investment long-term. Plus, adhering to specific formwork and concrete reinforcement guidelines protects the integrity of your structure. Skipping or rushing preparation increases the risk of structural problems, unexpected expenses, code violations, and safety hazards for your project. Following best industry practices, investing in expert advice, and maintaining strict quality control help you avoid common mistakes and ensure your foundation’s longevity. Skipping proper concrete foundation prep in commercial projects introduces serious risks—cracks, uneven flooring, and weak points in the slab often appear quickly. These issues can lead to binding doors, cracked walls, and expensive equipment that no longer sits level. Moisture seepage or drainage problems may also arise when the soil beneath the slab isn’t adequately compacted. Foundational errors create a ripple effect, leading to costly repairs and potential disruptions to business operations or tenant satisfaction. Cutting corners on prep work never proves beneficial when it comes to safety, building code compliance, or long-term durability. Industry best practices emphasize the importance of a thoroughly prepared foundation before any concrete is poured. The next section outlines what typically goes wrong and why proper preparation is essential. What Is Proper Site Preparation? On commercial concrete projects, site preparation lays the groundwork for a successful slab. It goes far beyond scraping away grass or shifting soil. The process begins with a thorough site inspection—reassessing the land’s topography, evaluating all slopes, and checking for potential obstructions. An even, properly compacted surface is critical to ensure structural stability and prevent future shifting or cracking. Smart, detailed planning at this stage safeguards the integrity of the foundation. Without this due diligence, cracks, settling, and other costly issues are far more likely to appear down the road. Beyond Just Clearing The Land Site preparation involves more than basic land clearing. All debris, roots, and brush must be fully removed, as leftover organic material can decay over time and create voids beneath the slab. A clean, well-prepared site is essential for protecting the foundation from erosion and prolonging the lifespan of the concrete. Implementing physical barriers and other best management practices helps prevent stormwater from washing away the site’s soil, ensuring long-term structural stability. Assessing Ground Conditions First Before work begins, it’s important to research the soil type at the site. Sandy, clay-heavy, or rocky soils each require distinct preparation methods—simple surface evaluations aren’t enough. Testing different soil layers with a shovel or probe helps determine stability. If the ground beneath the slab is weak, it can lead to cracking or settling over time. Conducting a proper soil analysis informs decisions about the appropriate concrete mix and slab thickness, ensuring a strong and lasting foundation. Why Soil Testing Is Non-Negotiable Soil tests determine whether the site contains loose fill, expansive clay, or other materials that may affect foundation performance. A qualified geotechnical engineer should review the results and recommend the most suitable preparation plan. Special attention is given to bearing capacity, compaction levels, and moisture content. Addressing these factors early helps avoid costly setbacks after the concrete is in place. Grading For Optimal Drainage The site is intentionally sloped to ensure rainwater flows away rather than underneath the slab. Proper drainage design is essential, with a gentle slope—typically no more than a 5 percent grade—directing runoff away from the structure. Even after initial grading, monitoring during heavy rainfall can reveal new pooling areas that need attention. Maintaining the correct slope reduces erosion and helps keep the slab surface dry and intact. The Essential Site Prep Checklist Whether for a big freeway job or a residential driveway, following a site prep checklist is critical for all commercial concrete jobs. This checklist takes you through each step to keep you on track with all of the moving pieces, including soil, submissions, and steel. Finally, it makes sure that everyone is working towards the same goal. A site prep checklist logs steps like soil testing, termite barriers, grading, and gear checks, so nothing falls through the cracks. In places with high termite risk, like parts of the Southeast, you need that barrier set below the finished floor line. You’ll learn important building transfer codes, including the International Building Code. Many of these codes mandate soil compaction to a minimum level of 90% of the dry density. If you don’t take these steps, you could end up with cracks or uneven slabs later. Thorough Site Clearing And Grubbing Ideally, you’d like to do this starting with a clean slate. That includes grubbing deep roots, clearing hard pan and weeds, and anything else that will eventually rot and sink. A site abandoned with stumps or brush will lead to soft spots in your slab. Crews need to maintain a clean workspace, remove rubble, and flag or paint areas for trench lines. Precise Excavation And Grading Work Avoiding the wrong depth, width, and shape when digging is key. Take, for instance, an extraordinarily simple scenario — pouring a warehouse floor. Off-level, ugly work will result in misaligned racks and machinery, causing a disaster down the line. Crews use laser levels to ensure proper grade. Proper grading will ensure less water pools on the site and will create an even slab. Achieving Correct Soil Compaction Proper compaction with rollers or plate compactors ensures the slab can bear weight. Your density gauge measures density so that you can make sure you