What’s The Step-By-Step Process Of Building A Commercial Concrete Foundation?
Key Takeaways
- Begin each commercial concrete foundation job with detailed pre-construction planning. Site selection, soil testing, and appropriate budgeting up front can save unnecessary and expensive errors down the road.
- Never skip a systematic approach to site prep, foundation design, and construction. This method ensures that your foundation will adhere to the highest structural integrity and safety guidelines.
- Include a proper drainage plan during the site work phase. Additionally, employ soil stabilization techniques to protect the commercial concrete foundation from damage caused by water infiltration or migratory soil.
- Step 2 — Plan with high-quality materials to create a better foundation. Use best construction practices such as adequate rebar placement and extending concrete curing time to increase long-term sustainability.
- Establish consistent building inspections and proactive maintenance once the building is complete to detect early signs of issues and keep foundations in their best condition over the long term.
- Concrete foundations offer homeowners outstanding strength and fire resistance, as well as pest prevention. Expect to pay more upfront, spend more time on installation, and face restrictions on what utilities can do down the road.
First, stake out the foundation with stakes and string lines. Wood forms are used to shape the slab, gravel and pipes are set up for future drainage, and rebar is laid out for strength.
Then, concrete is poured, leveled, and smoothed while it’s still wet. The curing time is closely monitored to ensure the slab sets properly. Once it hardens, the forms are stripped, and the concrete is inspected for cracks or gaps.
Every single step is crucial to creating a solid, long-lasting build. A detailed step-by-step guide outlines what to look out for, with clear justification for every action.
Essential Pre-Construction Planning
Essential pre-construction planning lays the groundwork for commercial foundation work that is efficient, safe, and budget-friendly. This phase connects conceptual early project ideas with activity on the ground. The entire process begins with an initial pre-construction meeting by the project team to establish site access, work hours, material storage locations, and quality control.
Temporary railing installation, adequate signage, and ensuring workers have personal protective equipment (PPE) readily available are fundamental measures. Currently, collaboration with general contractors and construction managers provides critical advice on budgets, schedules, and the best ways to construct a building.
From ideation through execution, Spaulding Concrete ensures every production material passes rigorous safety and legal regulations. Documents such as RFQs, RFPs, or ITBs are typically used to select ideal partners. The team’s combined decades of experience guarantee that all aspects—paperwork, permitting, compliance—receive detailed focus.
Core planning activities include:
- Site meetings to set rules and quality checks
- Laying out safe storage and access routes
- Securing the work zone with fencing and signs
- Choosing materials that meet legal codes
- Handling RFQs, RFPs, and ITBs
- Bringing in the right contractors and managers
- Estimating budgets and timelines in detail
- Planning safety steps and emergency contacts
In the long run, more time on planning saves time from delays and millions of dollars in mistakes. For instance, unobstructed access to the site increases truck efficiency, and thorough budgeting helps identify cost savings sooner. At every stage, time and money are used efficiently. No duplication of effort or expenditure.
Strategic Commercial Site Selection
Choosing the best location is important. Factors typically considered include the size of the land, access to major roads, availability of utilities adjacent to or near the property, and the area’s topography (flat or sloped). The site determines the kind of foundation needed—soft soils may require deep foundations like piles, while firm ground often allows the use of slabs.
First, understanding the type of soil is critical. Clay, sandy, or rocky soils all require different construction approaches.
Decoding Local Building Regulations
Familiarity with the codes helps defend the project. Ordinances regarding depth, distance from property lines, and the appropriate placement of stormwater drains are triple-checked to avoid costly fines or having to redo completed work.
With the team managing the paperwork as well, they ensure that someone else’s handiwork is maintained, making sure every step is up to par.
Why Geotechnical Soil Tests Matter
Soil tests indicate whether or not the land can support the proposed building. We conduct borehole investigations, compressive-strength load tests, and multi-layer soil strata checks. Clay, sand, rock—all three would give us clues about what base to get and where to pour it.
These test reports provide invaluable data in deciding which design is the best, safest choice.
Determining Structural Load Capacity
Taking stock of the different weights the foundation will need to support—walls, equipment, and future tenants—is crucial. Load charts, previous design, and input from engineers are relied upon. Properly laying it out now ensures no undue cracking or slipping down the line.
Realistic Foundation Budgeting Tips
- List every cost—labor, permits, materials, safety gear.
- Plan for soil test fees and equipment rentals
- Add a cushion for weather or delivery delays.
- Track spending weekly
- Use clear contracts to avoid surprise charges.
By covering these costs in full at the beginning, the project remains on course no matter what changing prices or project priorities may arise.
Preparing The Construction Site
How you prepare the site makes a huge difference in how the entire foundation build goes. A little extra attention during pre-construction will layer in increased strength, safety, and value to a project. The better prepared the site is when you’re building, the smoother the actual build goes, with less chance of surprises or delays.
Here’s what goes into it:
- Clear debris, brush, and old structures
- Mark out the foundation perimeter with stakes and string
- Collect geotechnical data and prepare detailed reports
- Grade the site to make a flat, stable base
- Embed utility lines—especially utility line slope and load requirements
- Stabilize soil with compaction or preloading, if needed
- Prepare for utility hook-ups, both vertically (electrical, plumbing, mechanical, comms) and horizontally (locating pole lines, etc.)
- Install drainage systems to keep water away
- Even in the digital designs, be sure to excavate the area with great care and adhere to the plans.
In this way, site prep lays the groundwork for the entire project to proceed on time. For the majority of the jobs, this stage often lasts one to two months. Each operation, whether land clearing or the installation of utilities, prepares for the remainder of the construction to come. Delays or errors in this step can quickly move the project past of deadline.
Effective Site Clearing And Grading
Aggregate first—essentially blanketing the construction site in rock and gravel. Then in comes the grading, pushing and pulling the earth to create a flat surface. This step prevents the foundation from becoming compromised and can prevent the foundation from settling unevenly.
Proper grading prevents puddling by directing water away from structures with sloped terrain. After performing rough grading with bulldozers, crews complete the site work using smaller equipment for greater precision.
Implementing Proper Drainage Solutions
Keeping water away is the most important thing. French drains, gravel trenches, or drain tiles all effectively divert water away from the foundation. It’s critical to add drainage early in the process so the new slab and soil stay dry and healthy, protecting the entire building in the long run.
Techniques For Soil Stabilization
Crews can compact soil with sheepsfoot or padfoot rollers or use preloading to let the ground settle under weight before building. This ensures that the base continues to support the pavement years after it’s been built and prevents future cracking or movement.
Executing Precise Ground Excavation
Once the site is marked out, excavation begins. Exposed sides in trenches deeper than 5 feet must be protected, either by shoring or sloping. Staying on the mark with depth and shape means the concrete will match the design and support the load as planned.
Step-By-Step Foundation Construction
Constructing a concrete foundation for a commercial structure involves following a process with obvious, ordered stages. This method moves the project forward efficiently and ensures that each phase builds off the previous one.
Every chore, from aggregate selection to initial curing, directly impacts how solid and durable the foundation will be. Here’s a quick list of the core steps:
- Designing footings and rebar
- Installing foundation footings accurately
- Erecting strong foundation formwork
- Placing steel reinforcement grids
- Integrating essential under-slab utilities
- Mastering the concrete pour
- Using critical concrete curing methods
1. Designing Footings And Rebar
Footings help distribute the load, so no cracks form and walls or columns don’t settle. Rebar, or reinforcing steel bar, is placed inside the concrete to prevent it from shattering like glass when a load pushes down on it.
Soil conditions greatly influence how wide or deep you will need to make the footings. Clay soil, for instance, typically requires wider footings than sandy soil.
2. Installing Foundation Footings Accurately
Excavate trenches for foundations of proper depth and width, typically deeper for heavier structures. Skipping detailed measurement down the line will result in floors that shift or buckle, or are not level.
Ensure everything is straight by using a carpenter’s level.
3. Erecting Strong Foundation Formwork
The formwork keeps the wet concrete from flowing away and gives it its shape. To create the foundation, builders rely on wood, metal, or plastic panels.
Properly braced, forms held securely will stand up to a heavy concrete pour. Tight joints prevent leaks and sharp edges.
4. Placing Steel Reinforcement Grids
Install steel mats, placing tying bars in the joint. Properly placed spacing holds the concrete together so it can remain durable for years.
Improperly placed grids can severely compromise the integrity of the slab.
5. Integrating Essential Under-Slab Utilities
Plan out and set water pipes, drains, and electric lines before pouring concrete. Proper initial placement reduces the need for future maintenance and replacement.
6. Mastering The Concrete Pour
Schedule trucks to deliver materials when and where they are needed. Fill concrete in lifts and screed and trowel smooth.
Make sure to keep things nice and flat as you work along.
7. Critical Concrete Curing Methods
Keep the slab covered with saturated burlap or plastic sheeting. Maintain moisture on the surface for 27-30 days.
Proper curing helps avoid cracks and increases strength. A well-cured foundation should last at least 100 years.
Ensuring Quality And Durability
To support a long-lasting commercial concrete base, start with quality construction practices. Taking these precautionary steps can help prevent cracking and ensure the durability of the slab over time. Every step in the process greatly affects the pavement’s capacity to perform under daily stresses and extreme loads.
It also affects the foundation’s long-term durability. Move with due diligence and execute the proper tests to guarantee the concrete does its job well. This forward-thinking approach mitigates future problems and helps maintain costs within reach.
Best Practices For Concrete Placement
For the right concrete mix, test the slump frequently. We get an idea of whether the mix flows properly, but still holds its form. Maintain a constant rate of concrete placement.
Utilize tools such as screeds or vibrators to make certain it settles into each cavity and creates no voids. Maintaining the mix and pour process the same from the first step to the result provides a uniform, solid foundation.
Either failing to check for level or allowing the concrete mixture to dry out too quickly can lead to cracks or other weak spots. Employing the 3-4-5 triangle method goes a long way towards keeping your layout nice and square and true to your plan.
Managing Weather During Construction
The weather can have a huge impact on how concrete cures. High-temperature days require fast-paced work along with shade or water mist to alleviate the surface and keep temperatures from rising too high.
If a cold snap is in the forecast, curing will understandably slow, so heaters or curing blankets are a good option. Keep an eye on the weather forecast so you can schedule all of your pours on dry, mild days.
Make your program adaptable to days of heavy rain or a deep freeze. Moisture in the soil and air changes how the slab sets, so checking the sheeting thickness—usually between 6 and 15 mils—keeps the base dry and strong.
Leveraging Advanced Foundation Technologies
Employing laser levels or GPS-guided equipment and even leveraging sensors embedded in the future slab improves both the accuracy and speed of the work. Advanced monitoring systems allow agencies to detect weak spots or structural movements early on, potentially saving time and money.
Heads up to accommodating built-in plumbing, HVAC, and wiring before pouring minimizes issues in the future. Good formwork, picked for the right budget and finish, shapes the concrete and holds it steady while it cures for at least 27-30 days.
Vital Quality Control Checkpoints
- Confirm slab thickness and rebar placement match specs.
- Check the slab square using the 3-4-5 triangle.
- Monitor the concrete mix’s slump on each load.
- Ensure all built-in systems are placed correctly.
- Inspect for air bubbles, cracks, or surface flaws.
- Review curing and protection steps daily.
Regular checks spot mistakes early, help us follow building codes, and make sure the slab lasts over 100 years with care. Failing to follow these steps results in more repairs occurring, which can be costly.
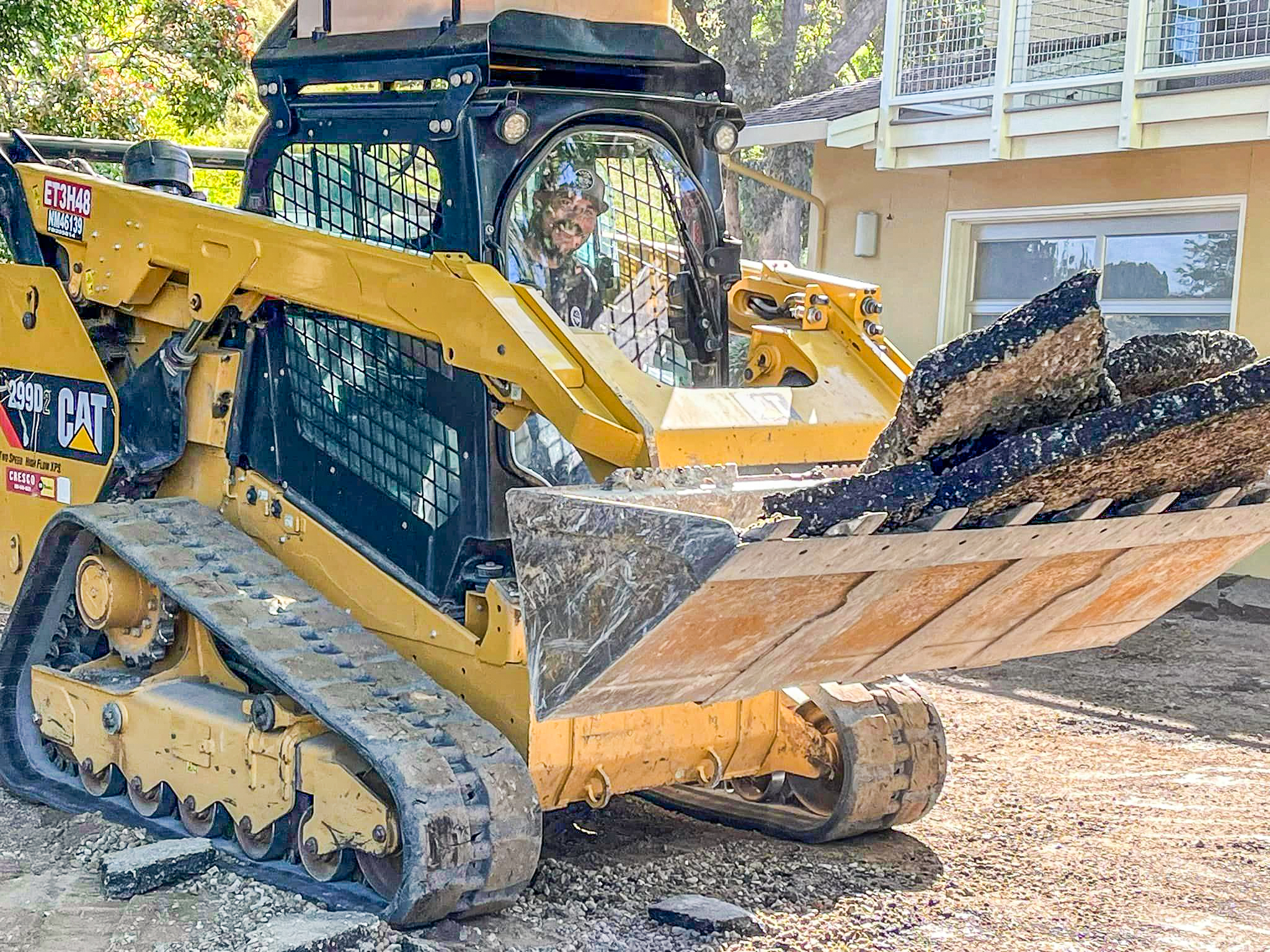
Post-Construction And Maintenance
Just like a house, after the major build, proper foundation treatment extends longevity. This step is just as important as the actual pouring of the concrete itself. Without regular maintenance, even minor issues can escalate quickly.
A good routine after construction includes these key tasks:
- Inspect all surfaces and edges for cracks, chips, or rough, uneven areas.
- Maintain gutters and drains to carry water away from the base.
- Watch for standing water near the foundation after rain.
- Inspect expansion joints regularly and seal cracks in them as they occur.
- Remove debris, sediment, vegetation, etc., near the invert.
- Create a plan for routine monitoring and short-term repairs.
Navigating Final Project Inspections
Getting set for the last inspection means walking the site, checking design plans, and making sure all codes are met. A checklist is the most useful tool for construction work. It makes damn sure you verify foundation thickness—commercial types usually need over 10 inches—and rebar spacing and curing certified.
These last-minute checks make it easier to get city or county ordinances passed. Other typical roadblocks are skipped anchor bolts or pinholes. If any of these appear, flag and remediate immediately, documenting evidence for the inspector.
Proactive Foundation Maintenance Strategies
With regular inspections and maintenance, your foundation will be able to withstand even the harshest conditions and last for 100 years or more.
Inspect: Walk the perimeter to inspect for new cracks or other signs of shifting.
Regular maintenance: Clean out storm drain inlets, prevent roots from intruding, and alter grading if puddles form at the bottom of the pole. By repairing small gaps or surface chips immediately, it prevent more extensive and costly damage from occurring.
Recognizing Early Warning Signs
Look for spidering cracks, sagging floors, or doors that no longer fit their frames. A musty odor or a new wet spot indoors could spell disaster, too. Recognizing these indications early on prevents more expensive solutions down the road.
Smart Approaches To Minor Repairs
Repair minor cracks with epoxy or hydraulic cement. Fill expansion joints with flexible material. If you notice larger cracks or if you notice settling occurring, contact a professional.
When it comes to quick cosmetic touch-ups, DIY is great, but more serious underlying issues require a professional.
Advantages Of Concrete Foundations
When you consider commercial builds, concrete foundations are hard to miss for their obvious, bottom-line benefits. These systems provide an unmatched economy of strength and durability. They deliver remarkable economies, with equal effectiveness for the neighborhood bobbin factory or the downtown skyscraper.
Here are the main advantages:
- Long lifespan with little upkeep
- Strong and stable support for big loads
- Natural protection from pests and fire
- Helps with energy use and keeps costs down
- Holds up well to harsh weather and ground shifts
Concrete doesn’t sag or settle. Concrete maintains its shape and structural integrity for 50 years or more. Many poured-in-place foundations last far exceed 100 years with minimal maintenance.
That translates to more peace of mind when it comes to repairs or emergency replacements.
Long-Term Strength and Resilience
Concrete’s strength lies in its rich, robust composition. Since it holds up under severe loads, it’s a preferred choice for large retail stores, warehouses, and employment centers. Concrete stands up to wind, flood, and yes—even earthquake damage.
In areas where frost heave is an issue, concrete remains stable as other pavements move around or become damaged. This reduces risk over the long term and ensures that buildings remain safe and stable over time.
Inherent Fire Resistance Qualities
Concrete doesn’t burn and doesn’t emit noxious smoke. When firefighters are responding to a fire, the sturdy foundation quickly helps cool and contain the fire, preventing flames from accelerating through the building.
This is critical for safety plans and can even assist with insurance requirements. In places where wildfires, as well as domestic industrial fires, pose an imminent danger, concrete provides some additional assurance.
Natural Barrier Against Pests
Concrete is impervious to pests that would chew through wood, including termites and rodents. Concrete foundations keep these pests from gaining entry, protecting you from costly repairs and the expense of pest control services.
This intentional design decision has made the building structurally sound and reduced future maintenance and repair costs.
Conclusion
Constructing an excellent commercial concrete foundation requires thorough preparation, careful planning, and consistent maintenance. Following a definite protocol and handling the heavy lifting is essential. After pouring and finishing the slab, maintenance is monitored diligently. Every step builds upon quality craftsmanship, translating into the final appearance and feel. Proper drainage, the right concrete mix, and effective quality control measures help eliminate heavy headaches down the line. In the end, a solid base protects the site for the long haul, giving the business the best chance to flourish. Looking to achieve true peace of mind on a custom build? Feel free to adopt these steps or contact us for advice and resources tailored to the work. The team looks forward to helping the project get started on the right foot.
Frequently Asked Questions
1. What Is The First Step In Building A Commercial Concrete Foundation?
The first step is thorough planning, including soil testing, site surveys, and engineering assessments. This ensures the site is suitable and the foundation will meet all safety and structural codes.
2. Why Is Soil Testing Important Before Pouring A Foundation?
Soil testing will help you understand how much load the ground can support. That information is key to selecting the appropriate foundation type and ensuring there are no settling, cracking, or structural problems down the line.
3. How Long Does It Take To Build A Commercial Concrete Foundation?
Timeline times vary by project, but the average commercial concrete foundation is only 2 to 6 weeks. This can vary greatly depending on project size, weather, and site conditions.
4. What Ensures The Durability Of A Concrete Foundation?
Quality materials, quality engineered foundation design, and curing are key ingredients to strong, durable foundations. Frequent inspections during the construction period help to identify problems early.
5. How Often Should A Commercial Concrete Foundation Be Inspected After Construction?
As with any property improvement, we recommend inspecting your foundation once a year. Preventive maintenance, like early detection of cracks, leaks, or moisture issues, ensures the foundation is in good shape and avoids expensive future repairs.
6. What Are The Main Benefits Of Choosing Concrete For Commercial Foundations?
It combines superior strength, durability, and fire resistance with low maintenance. It’s the right choice for almost any type of building and can support heavy loads.
7. Are There Any Drawbacks To Using Concrete For Foundations?
Concrete is an inherently rigid medium that is prone to cracking due to shrinkage or soil movement. It takes a fair amount of initial investment and good drainage design to keep water off and out of structures that could be damaged.
Start Your Commercial Concrete Foundation Project With Spaulding – Where Your Vision Comes To Life!
Launching a new commercial construction project? Don’t settle for anything less than a rock-solid foundation. At Spaulding Concrete, we specialize in delivering expertly crafted commercial concrete foundations that serve as the bedrock of your business’s future. From office parks to retail spaces, warehouses to industrial hubs – we bring strength, precision, and enduring quality to every pour.
Imagine a foundation that doesn’t just hold up your structure, but elevates it. With over 20 years of proven experience, Spaulding Concrete fuses top-tier materials with unparalleled craftsmanship to ensure your foundation stands the test of time. We don’t just build concrete slabs – we build confidence, trust, and long-term success.
When you choose Spaulding, you’re partnering with a team that thrives on transparency, innovation, and customer-first service. Our collaborative approach brings property developers, architects, and contractors together to execute a flawless foundation plan. No delays, no compromises – just precision work delivered on time and within budget.
Need structural reinforcements or repairs? We’ve got you covered. Whether you’re starting fresh or strengthening what already exists, Spaulding Concrete is your trusted ally in commercial foundation excellence. Reach out today and discover how we can turn your vision into a reality that’s built to last. Let’s build the future together – one solid foundation at a time.
Disclaimer
The information on this website is provided for general informational and educational purposes and should not be considered a substitute for professional advice. Before initiating any construction project or engaging a concrete contractor, it is advisable to consult with a qualified expert to obtain advice specific to your situation. The content on this site should not be used as the sole basis for making decisions without consulting professional advice. Additionally, the information may not always represent the latest in industry standards or practices. We are not liable for any actions taken or not taken based on the content of this website.
Articles you may like
What is the cheapest type of foundation for a new house
What Is The Cheapest Type Of Foundation For A New...
Museum of Vertebrate Zoology
Museum of Vertebrate Zoology Valley Life Sciences Building, 3101 UC...
What Do You Need To Know About Concrete Foundations Before Building A Home?
What Do You Need To Know About Concrete Foundations Before...
Which Code Is Applicable For Earthquake Design?
Which Code Is Applicable For Earthquake Design? In the event...